Crusher Rotor
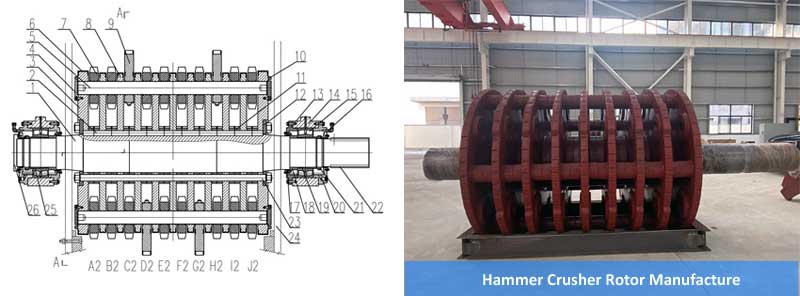
Crusher Rotor Assembly from AGICO
Agico mainly supplies rotor assembly for hammer mill and Impact crusher, which is the major working part of a crusher equipment. With rich experience in design and manufacture rotary assembly, AGICO offers rotary assembly customization service according to crusher model and raw materials.
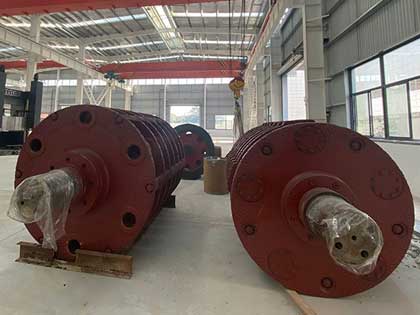
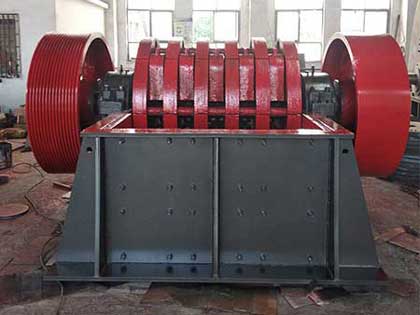
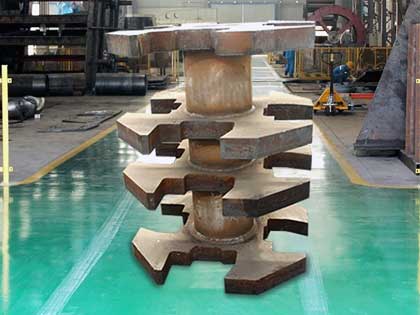
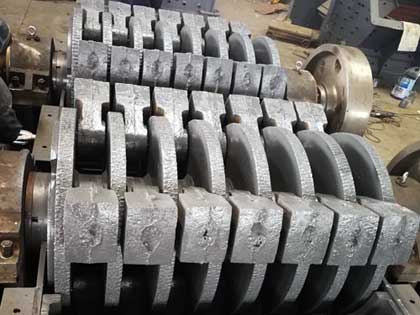
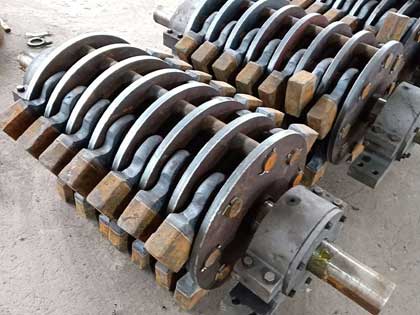
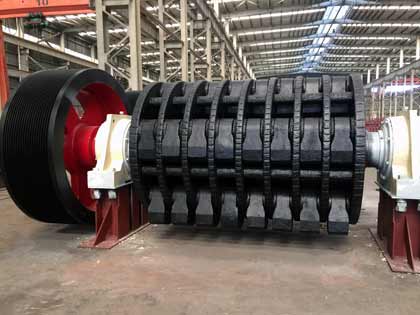
Hammer Crusher Rotor Customization Service
For hammer mill rotors, based on the different production projects,crushed materials and different requirements for quality, AGICO can customize best design crusher rotors for customers according to their requirements, called rotor customization service.
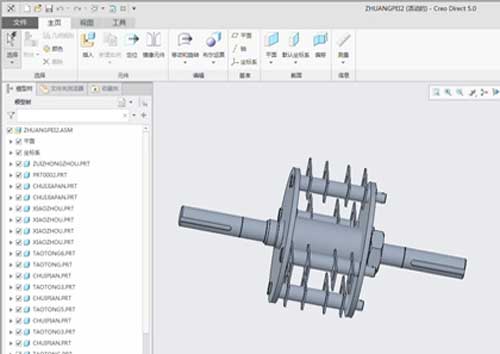
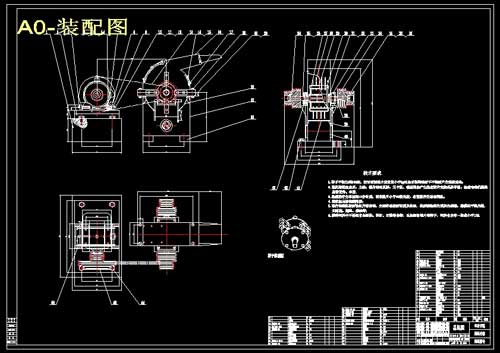
Customer Visit Crusher Rotor Factory

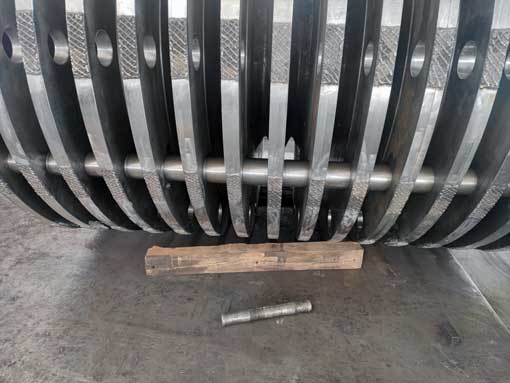
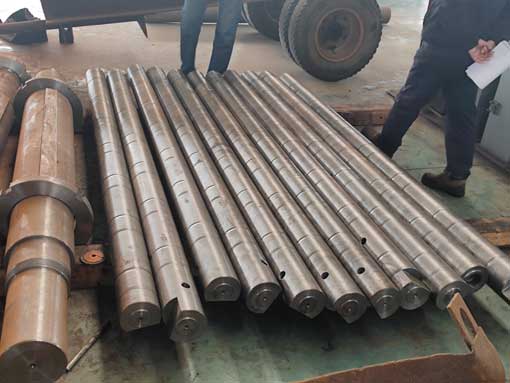
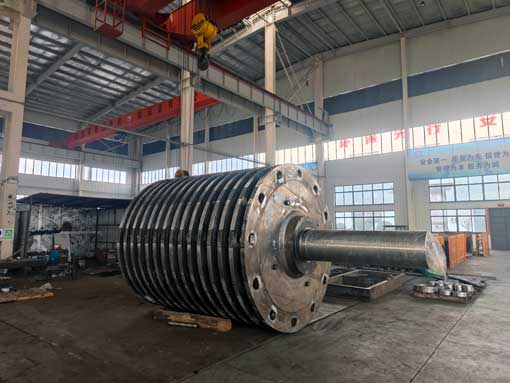
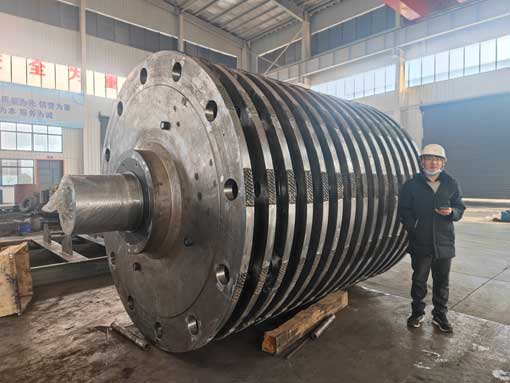
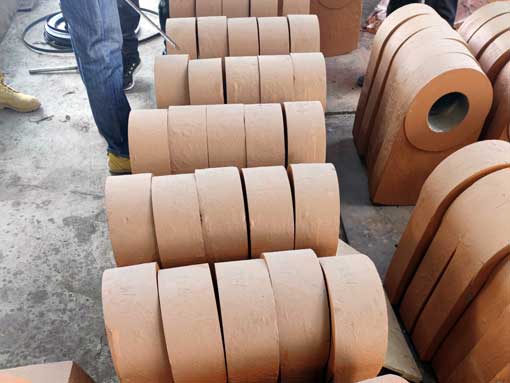
- Crusher Rotor Drawing To customize the corresponding rotor for the equipment, customer only need to provide the corresponding crusher rotor drawing and crusher equipment model, and the rotor can be customized for you quickly.
- Add Protective Facilities For crusher rotors of the same model, design requirements for specific parts can be provided. For example, the rotor hammer plate can be modified to add corresponding protective facilities or protective points can be added to the hammer head.
- Upgrade plan For customized crusher rotors, technical personnel will be arranged to visit and review the usage regularly, and timely improvement plans will be made based on the usage status to ensure the effectiveness of the crusher rotor.
Common Design - Rotor Assembly of Hammer Mill
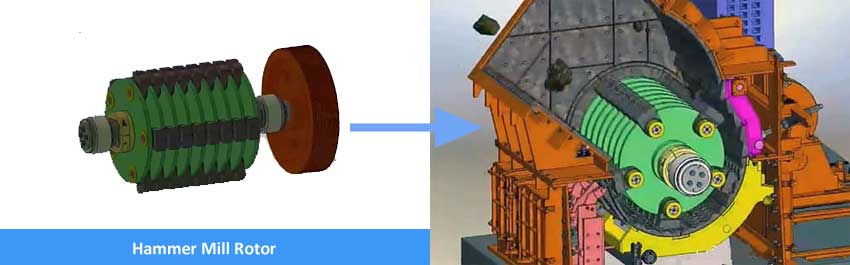
The rotor assembly is the core of the hammer mill, and its structural forms can be divided into aligned and cross arrangement.
- The aligned arrangement means that the hammer heads of the crusher are arranged in alignment with each other. Depending on the size of the rotor specifications, they are divided into 4-6 rows on the circumference, with 7-11 crushing hammer heads per row.
- The cross arrangement means that the hammer heads of the crusher are arranged in a crisscross manner.And they are divided into 4-6 rows on the circumference, with 6-8 crushing hammer heads per row.
Classification of Rotor in Hammer Mill
The main working part of the hammer mill is the crusher rotor, which crushes materials by the impact of high-speed rotating hammer heads. There are many types of hammer mills classified by different structural characteristics as follows:
Hammer Mill Rotor Type | |
---|---|
Rotor Number | single rotor and double rotor |
Hammer Arrangement | single-row and multi-row types |
Hammer Connection | Fixed and Active type |
Rotation Direction | irreversible rotor and reversible rotor |
Rotor Assembly Components of hammer mill
The rotor of the hammer mill is its main working part, and its performance directly affects the working efficiency of the crusher. The rotor is composed of a main shaft, hammer frame, and hammer heads.
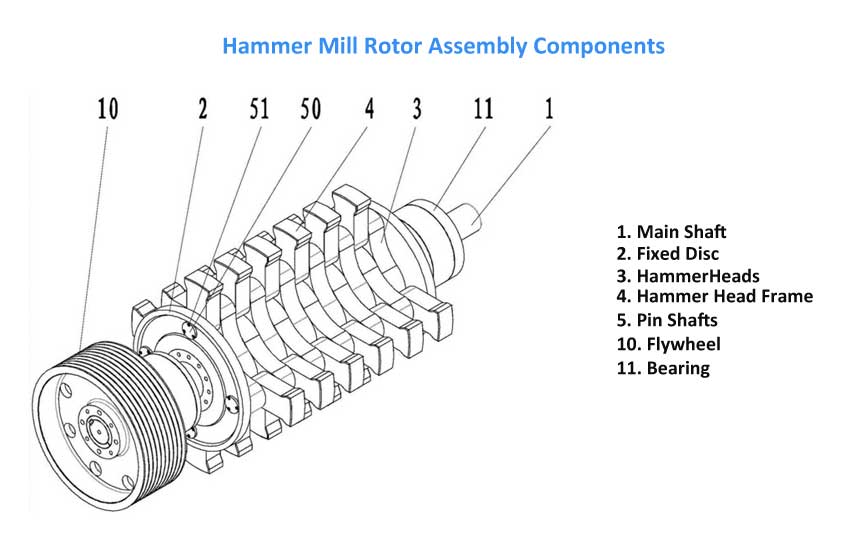
-
Main Shaft: The main shaft is the main component that supports the rotor of the hammer mill. It bears the weight and impact force from the rotor and hammer heads, so the material of the main shaft must have high strength and toughness. When designing the rotor of the hammer mill, 35SiMnMoV steel can be used for forging. The cross-section of the main shaft is circular, with a maximum diameter of 130mm and a bearing diameter of 80mm. The hammer frame is connected to the shaft by a flat key.
-
Hammer Frame: The hammer frame is used to suspend the hammer heads and does not play a role in crushing materials. However, during the operation of the hammer mill, the hammer frame will still be subject to wear and tear due to the impact and friction of the ore. Therefore, the hammer frame must also have a certain wear resistance. There are 12 hammer frame pin holes on the hammer frame, divided into two groups.
-
Hammer Head: The hammer head is the main working part of the hammer mill. The weight, shape, and material of the hammer head have a great impact on the production capacity of the crusher. The kinetic energy of the hammer head is proportional to its weight, but the weight of the hammer head should be moderate. In addition, it is important to choose the appropriate material for the hammer head. High manganese steel can be used to cast the hammer head, and heat treatment can make it have high wear resistance and a longer service life. In production, it is necessary to pay attention to the wear of the hammer head, inspect it regularly, and replace it in time.
-
Flywheel: The main function of the flywheel is to store the required kinetic energy of the rotor of the crusher during operation. This improves the efficiency of the crusher, reduces the power consumption of the crusher, and ensures that the motor is not overloaded during normal operation. When the crusher is fed too much or large pieces of material enter, the flywheel releases its stored energy to improve the crushing capacity and avoid overload occasion.
Performance characteristics of crusher rotor:
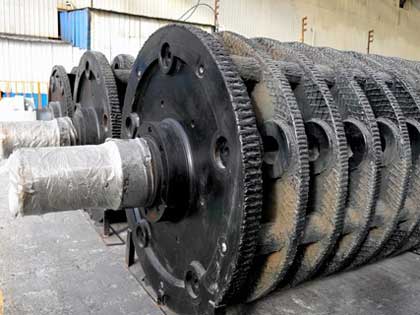
-
Protective rings extends the service life of crusher rotor.
Under the impact of stone in the crusher, the edge of the rotor hammer plate is easily worn, and the rotor must be replaced after wear. To address this issue, AGICO introduced protective ring technology, which greatly improves the life of the rotor. After the edge of the hammer plate is worn, the protective ring can be replaced by simply removing the bolts without replacing the entire rotor. -
The diameter of the hammer frame plate is increased, and the hammer head can rotate 360 degrees。
Reducing direct impact between the hammer head and the spacer during the flipping process. This solves the problem of traditional hammer mills, where the spacer is easily broken or loosened by the hammer head, the hammer head falls off, and the hammer shaft is easily broken. -
The chromium-manganese composite casting hammer head
This design improves the impact resistance of the hammer handle and the crushing performance. Based on finite element structural analysis and simulation, stress analysis cloud maps clearly show that the danger zone of the crusher rotor is mainly distributed in the handle of the hammer head, the hammer shaft hole of the hammer plate, the external support of the hammer plate, the hammer shaft, and the shoulder of the main bearing position.
Improved design of crusher rotor:
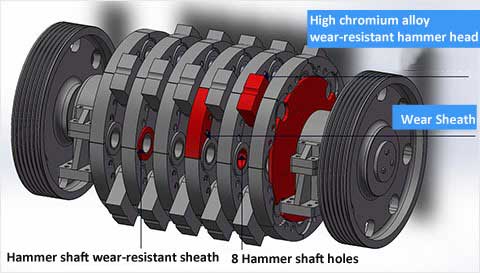
- Advanced finite element analysis technology is used to effectively improve the design of the crusher rotor.
- High Strength Steel Weakened areas on the stress analysis cloud map of the crusher rotor are strengthened by using high-strength, high-quality alloy steel.
- Crusher Rotor Surface Design The surface of the crusher rotor is designed with titanium alloy armor, which reduces stress concentration in the hammer plate and end plate, strengthens its strength, effectively prevents breakage problems, and can effectively prevent the crusher from getting stuck, thus doubling the life of the crusher rotor.
- Variable moment of inertia design is used to effectively improve crushing efficiency, increase crusher output, and reduce fineness by 20-30%.
- Improved Shaft Hole Design The shaft holes around the end plate and hammer plate of the crusher rotor are thickened and extended to the connecting bolt holes. The thickened parts have crescent-shaped grooves that facilitate the rotation of the crusher hammer head. The hammer plate and end plate are directly assembled on the main shaft.
Crusher rotor repair Maintenance
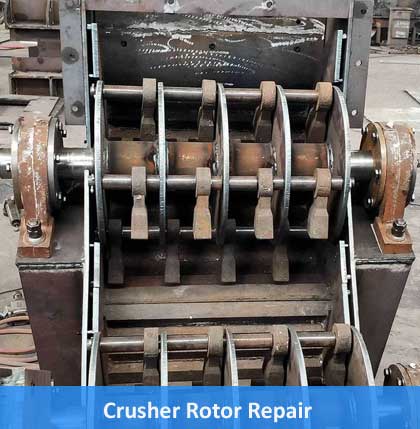
Main Failure Modes
The main failure modes of crusher rotors with transitional wear are severe wear of the hammer disc shaft hole and outer edge, hammer shaft fracture, hammer disc cracking, malfunction of locking device, spindle displacement, bearing heating, and in severe cases, bearing damage, spindle deformation, and even fracture.
Solutions
The main contents of major overhaul of crusher rotors include inspection and bending repair of hammer and main shafts of hammer mills, inspection and repair of locking devices, repair or replacement of rotor hammer disc outer edges, repair and replacement of hammer heads and grading, cleaning and maintenance of bearings, bearing seats, and sealing devices.
Crusher rotor repair technology:
-
Advanced rotor repair technology. The rotor repair uses hard surface surfacing technology, bimetal centrifugal casting technology, WHM secondary welding technology, tungsten-titanium alloy technology, finite element analysis technology, etc.
-
Good performance after repair. The repaired crusher rotor has good dynamic balance, long service life of wear-resistant parts and main bearings, and can effectively reduce maintenance times and maintenance costs.
Crusher rotor quality control at AGICO
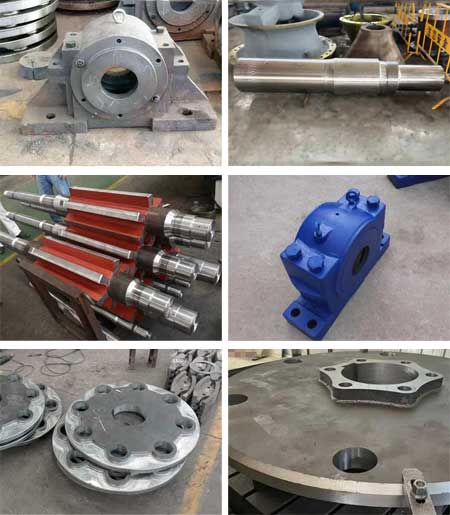
-
Retaining ring
On the rotor disc, we use ZGMn17Cr2 material for the retaining ring, which does not require welding rods. The retaining sleeve is fixed with a snap ring pin shaft, which is easy to replace, reducing labor intensity and increasing startup time. Adding a retaining ring to the hammer disc mainly adds an alloy layer on the outer surface of the hammer disc, which is made of materials composed of various rare elements. This can make the hammer disc have high damage resistance and avoid direct impact of materials on the hammer disc. -
Hammer shaft hole
Our rotor is designed with eight hammer shaft holes, using four hammer holes and reserving four spare hammer holes, making our rotor into two rotors. -
Hammer Shaft
We use rough turning, quenching and carburizing, and then precise turning to improve the strength, toughness, and degree of the hammer shaft. -
Hammer head
We use a hot composite bimetal high-chromium alloy hammer head, which has high strength and can crush limestone up to 800,000-1.2 million tons. -
Main shaft
We use 42CrMo material for rough turning, quenching treatment to increase strength and toughness, and then precise turning to mill a square fitting surface in contact with the hammer disc on a gantry boring and milling machine. Compared with traditional rotors, the service life is greatly improved.
Difference between hammer mill and Impact Crusher Rotors
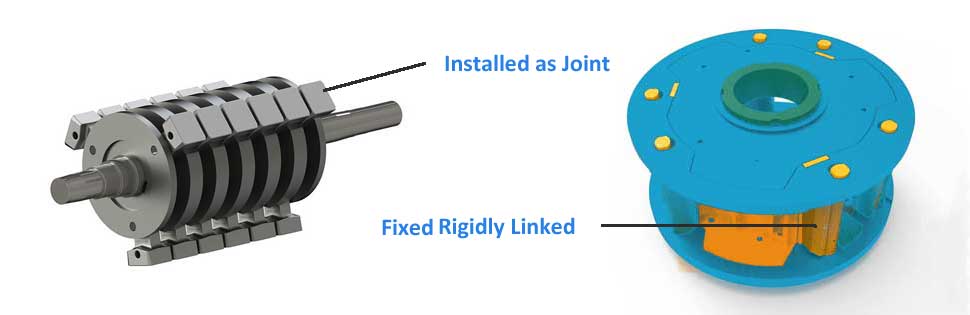
The plate hammers and rotors of impact crushers are rigidly linked, with it being fixedly installed on the rotor. During crushing, the inertia of the entire crusher rotor is fully utilized to impact the material, not only crushing the material, but also providing a high speed and kinetic energy. However, the hammer heads of hammer mills are single and are limited in speed and kinetic energy.
How to Design rotor assembly
Designing the rotor assembly requires mechanical design first. After completing the mechanical design, the structural design of the rotor assembly should be carried out. Although the structures of the rotor parts of different types of single-stage hammer mills are different, they generally have the following common points in design:
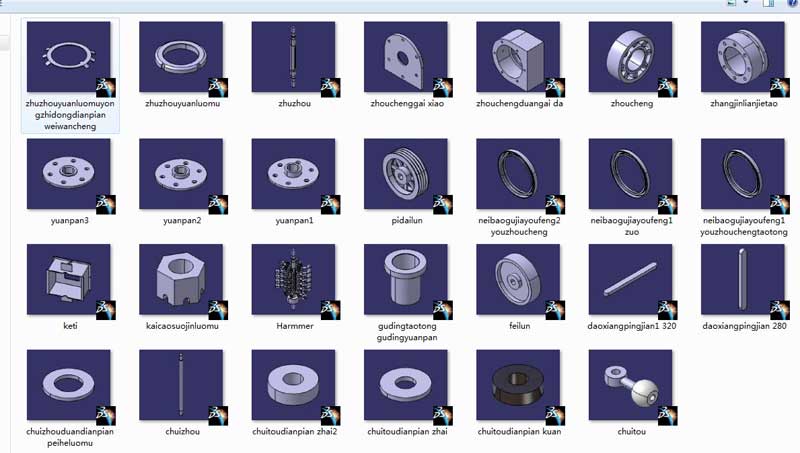
-
The safety and reliability of the crusher design are paramount. Under high-speed operation, the hammer head strongly impacts the material, making the force on the rotor body extremely severe and complex. Therefore, the equipment should always be in a safe operating state within the specified maintenance period.
-
To reduce metal consumption and production costs, the number of hammerheads should be minimized while meeting the crushing function. Since the number of hammerheads in three rows is less than that in four rows, three rows should be selected instead of four rows if possible.
-
After determining the quality of the hammerhead, comprehensive analysis and optimization selection should be carried out. This requires consideration of the width of the hammerhead, which is conducive to strengthening the crushing effect, but the gap between the hammer discs will increase, and the crushed material flow will be short-circuited through this channel, which will reduce the proportion of fine powder and worsen wear.
-
The hammerheads of the crusher wear severely during production, so the fixation and replacement of the hammerhead and hammer plate should be considered during design. The hammer plate should be easily secured without opening the machine shell during the shift changeover.
Maintenance of Impact Crusher Rotor
- Reasonable adjustment of the matching relationship between components
The rotor bearings of the impact crusher mainly bear impact loads during the crushing process, and the loads on different positions of the rolling elements are not the same. The double-row centripetal spherical roller bearings have the advantages of strong load-bearing capacity and good self-aligning performance. Therefore, this kind of bearing is used as the rotor bearing of the impact crusher, and the inner ring should be fitted tightly to avoid the phenomenon of a certain point staying on the maximum stress point. The outer ring should be fitted loosely, which may cause slight movement under impact force, thus increasing the maximum stress point and prolonging the life of the outer ring.
In addition, the calculated life of the rotor bearing should be about 5000-10000 hours.
- Selection of wear-resistant materials for the rotor and thickening of the rotor discs on both sides
Regardless of the production capacity of the impact crusher, the number of rotor discs, or the size of the equipment, the rotor discs on both sides of the rotor are generally the most severely worn parts. Therefore, the rotor discs on both sides are also the focus of maintenance and repair of the impact crusher.
Thickening the two sides of the rotor disc can improve the wear resistance to some extent. When the disc is welded, thickening can also prevent deformation during the welding process. However, even with the changes of thickening and the selection of wear-resistant materials for the rotor disc, the wear of the disc cannot be completely avoided, so daily maintenance and repair are still indispensable.
Considering the cost, most users choose the repair process of welding and coating first, that is, the repair personnel regularly carry out welding and coating treatment on the disc. Firstly, the worn parts of the disc are repaired with iron-chromium-boron wear-resistant welding rods to restore the worn parts to the original shape as much as possible, and then coated with tungsten carbide wear-resistant welding rods. This method can not only ensure the practical and durable properties, but also consider the economy.
- Improving the balance accuracy of the rotor
The impact crusher rotor has a large mass and high speed. The casting deviation of the rotor body and the quality deviation caused by the installation of the plate hammer will cause unbalanced centrifugal force when the rotor rotates. This centrifugal force will cause forced vibration of the machine, resulting in damage to bearings and other components. Therefore, the rotor of the impact crusher must undergo a balance test.
①When the diameter of the rotor body is small, the balance can be achieved by changing the mass of the blocking plate on both sides of the rotor body.
②When the diameter of the rotor body is large, the counterweights can be welded on the outer wall of the rotor body. To prevent the counterweights from falling off during vibration, several rows of grooves can be cast at appropriate positions and the counterweights can be embedded and then welded. This method is both firm and beautiful.
- Adjustment of internal clearances
The internal clearances of the impact crusher mainly refer to the clearances between the rotor body and the impact plate, apron, and hammerhead. The sizes of these clearances are related to whether there are materials accumulated near the apron and safety door. If there are materials, and the hammerhead cannot push the materials down from the apron, the hammerhead will be seriously worn by friction. Therefore, in the process of use, the clearances of various parts must be adjusted frequently to keep them within an appropriate range.