SAG Mill
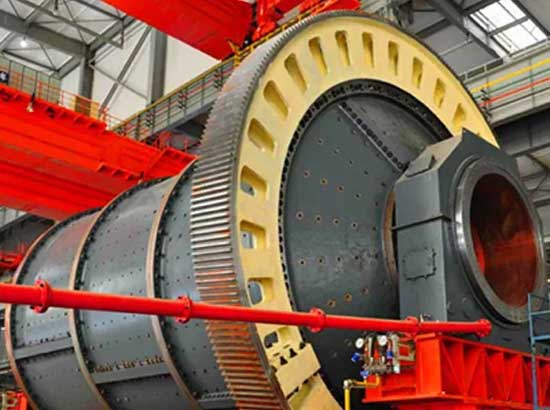
AG MILL or SAG MILL introduction
AG MILL(autogenous grinder) or SAG MILL(semi-autogenous grinder), also known as No media mill, , which works principle same as ball mill , the difference is even greater its cylinder diameter, without a ball or any other grinding media, the use of the cylinder body is pulverized material itself as a medium in the cylinder body continuously and mutually impact grinding mill to achieve the purpose of stripping. Sometimes in order to increase processing capacity, it can be added to a small amount of steel balls, typically only 2-3% since the effective volume of the mill. The most important feature of AG mill or SAG mill is to feed raw ore from the stope or after crushing the ore to the mill directly. Typically certain mineral grain size ratio to the mill or rod mill. Since AG mill or SAG mill can grind the material to -0.074mm (its content once accounted for more than 20% to 50% of the total product). Crushing ratio up to 4000 to 5000, rod mill ten times higher than the ball mill,. AG mill or SAG mill is the new grinding equipment,have crushing and grinding two functions. It uses the material to be grinding as the medium itself, achieve mutual crushed by the impact and grinding effect. Since the mill is also called a free media mill.
The SAG mill also kown as medium-free grinding mill. The ore from the stope or the coarsely crushed ore can be directly fed into the mill. The biggest speciality of the SAG mill is that the crushing ratio is large, the input size of the grinding material is 300~400mm, sometimes even larger, and the output size can reach 0.1mm minimum, the crushing ratio can reach 3000~4000, and the inout size of ball mill is between 20-30mm, the output size is 0-3mm.
SAG Mill Working Principle
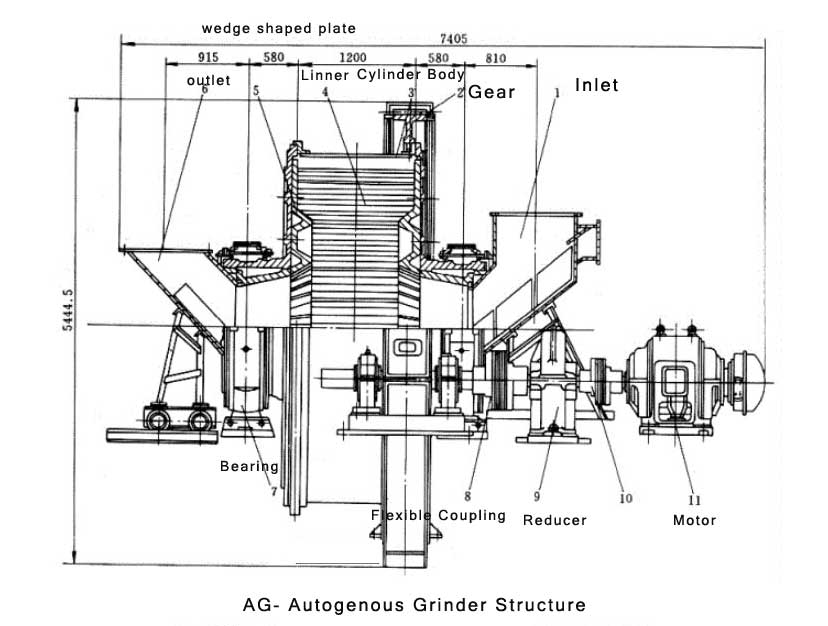
The SAG mill is a new type of grinding equipment that combines both crushing and grinding functions. It uses the material itself as the medium to crush by mutual impact and grinding. The SAG mill has two kinds of dragging modes: variable speed and different power fixed speed. Some SAG mills are also equipped with micro-motion devices. In order to facilitate the maintenance, there is acylinder jacking device; for the large mill, in order to eliminate the static resistance torque at the start, a modern advanced technology such as a hydrostatic bearing is adopted to ensure the mill can operate safely.
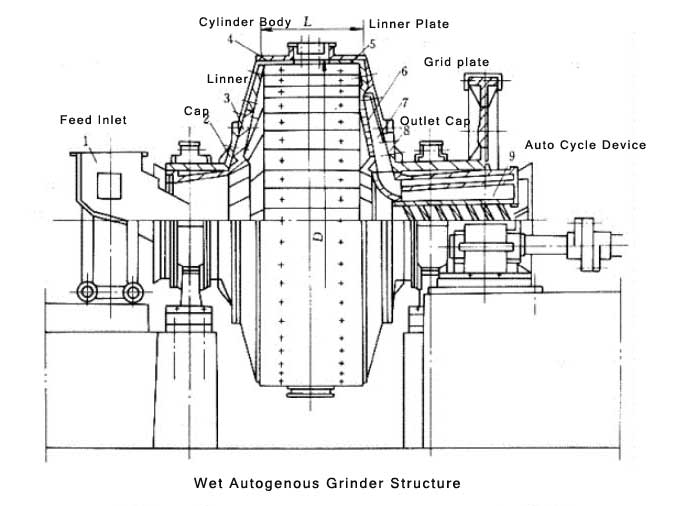
The wet self-grinding system consists of a SAG mill, a particle size control operation, a secondary grinding equipment, and a hard-to-grain-level processing facility. Usually the mineral is fed into the mill bar at a certain ratio. The self-grinding machine can grind the material to 0.074mm at a time, and its content accounts for 20% to 50% of the total amount of the product. The crushing ratio can reach 4000~5000, which is ten times higher than the ball mill and rod mill.
Application range of AG MILL or SAG MILL
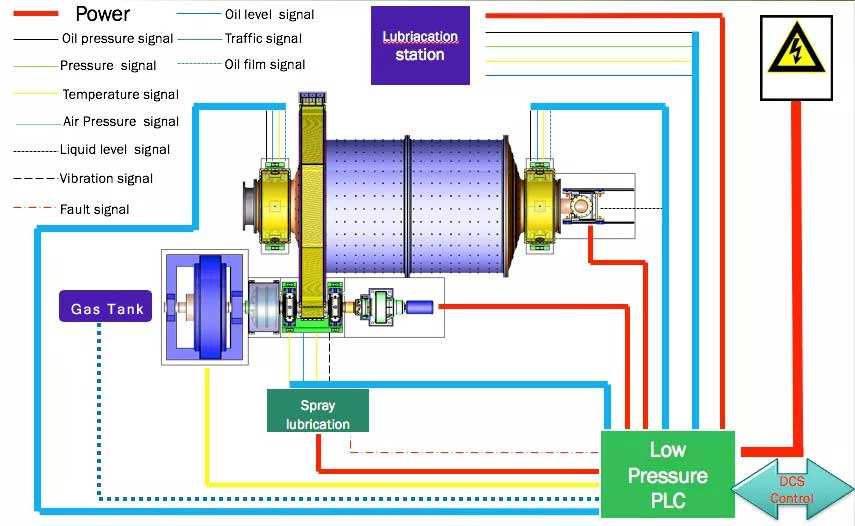
Since AG MILL or SAG MILL mill can handle any nature, especially when pulverized asbestos, iron ore, copper ore, limestone, gold, manganese and other materials better. Since the most important feature of the mill is crushing ratio, which to mine generally 300-400 mm (special circumstances can be as large as 910 mm), after autogenous grinding can be ground to a particle size of 0.1 mm or less. Crushing ratio up to 3000-4000, compared with a ball mill or rod mill grinding ratio is ten times larger. Because of this the most important feature, so that autogenous grinding technology has the following main advantages:
- Reduce crushing, grinding and transportation equipment, simplify the process, small space taken, less investment in infrastructure;
- Saving grinding media consumption, reduce power consumption, reduce operating personnel, reduce equipment operation and maintenance costs;
- Wide range, without restricting the types of ore;
- Ore is to grinding by itself, selective grinding stronger, less than crushed, therefore, easy sorting, will help to improve beneficiation indicators improve concentrate grade and recovery.
Feature of wet or dry AG mill or SAG mill
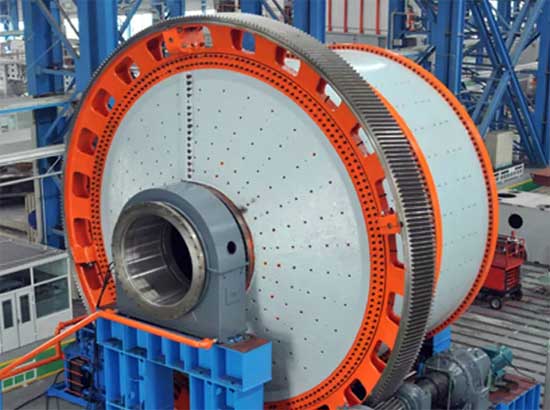
Dry and wet autogenous grinding mill from common are: large feed size, crushing ratio up to about 100 to 150; crushing grinding process can be simplified, saving equipment, saving infrastructure investment, and production management fees are lower. They have advantages and disadvantages, what kind of autogenous grinding mode uses as well, it should be determined in accordance with specific conditions. Advantages of dry autogenous grinding are: Production capacity than wet autogenous grinding high, no water transportation, which for drying or profile dryland areas prone freeze, apply dry-autogenous grinding is more appropriate. Dry than wet autogenous grinding mill liner wear from light. The disadvantage of dry autogenous grinding is: for high mud, water large (no more than 4% -5%) of ore must be dried, and therefore should not be used in southern China are dry autogenous grinding. In addition, since the mill is dry transport by air flow, air classification, and therefore the larger problem of wearable systems, dust and other aspects of power consumption. Advantages of wet autogenous grinding is: except for a few hard ore, the vast majority of metal ores, especially the larger density of iron ore, can be applied wet autogenous grinding. Power consumption is also lower than the wet from the dry mill from grinding, grading system and its ancillary facilities is relatively simple, since wet grinding job does not produce dust, environmental pollution, its investment is also lower than the dry autogenous grinding. The disadvantage of wet autogenous grinding are: low production capacity, liner consume more, the harder ore to consider measures to eliminate "stone" (hard grinding particles) accumulation. It should be noted that since the development of the mill at an early stage autogenous grinding mainly dry, then wet autogenous grinding dominant. The current development trend autogenous grinding dry from wet autogenous grinding mill may be replaced.
/>AG Mill or SAG MILL technical parameters:
Model | Diameter of cylinder (mm) | Length of cylinder (mm) | volume (m3) | Speed of mill (r/min) | transmission | power kw | Speed of motor r/min | oversize(L×W×H)m | weight(t) |
MZ24×10 | 2400 | 1000 | 4.5 | 22 | edge | 55 | 740 | 7.8×3.5×3.3 | 18.5 |
MZ32×12 | 3200 | 1200 | 9.2 | 18.2 | 160 | 740 | 8×4.1×3.7 | 32.8 | |
MZ40×14 | 4000 | 1400 | 16.6 | 17.6 | 250 | 735 | 11.5×5×4.7 | 63 | |
MZ55×18 | 5500 | 1800 | 34.6 | 15 | 800 | 167 | 14.1×7×6.3 | 178 | |
MZ64×33 | 6400 | 3300 | 107 | 12.8 | 2000 | 200 | 23×10.3×9 | 306 | |
MZ75×25 | 7500 | 2500 | 107 | 11.4 | 2000 | 200 | 23×10.5×10 | 355 | |
MZ85×40 | 8500 | 4000 | 225 | 102 | 4850 | 200 | 27×14.2×12.9 |
AG Mill or SAG MILL Specification:
Model | Rotation speed of bucket(r/min) |
Weight of ball (t) |
Feed size (mm) |
Discharge size(mm) | Production(t/h) |
power (kw) |
weight(T) |
Φ900×1800 | 38 | 1.5 | ≤20 | 0.075-0.89 | 0.65-2 | 18.5 | 3.6 |
Φ900×3000 | 38 | 2.7 | ≤20 | 0.075-0.89 | 1.1-3.5 | 22 | 4.6 |
Φ1200×2400 | 32 | 3.8 | ≤25 | 0.075-0.6 | 1.5-4.8 | 45 | 12.5 |
Φ1200×3000 | 32 | 5 | ≤25 | 0.074-0.4 | 1.6-5 | 45 | 12.8 |
Φ1200×4500 | 32 | 7 | ≤25 | 0.074-0.4 | 1.6-5.8 | 55 | 13.8 |
Φ1500×3000 | 27 | 8 | ≤25 | 0.074-0.4 | 2-5 | 90 | 17 |
Φ1500×4500 | 27 | 14 | ≤25 | 0.074-0.4 | 3-6 | 110 | 21 |
Φ1500×5700 | 27 | 15 | ≤25 | 0.074-0.4 | 3.5-8 | 132 | 24.7 |
Φ1830×3000 | 24 | 11 | ≤25 | 0.074-0.4 | 4-10 | 180 | 28 |
Φ1830×6400 | 24 | 23 | ≤25 | 0.074-0.4 | 6.5-15 | 210 | 34 |
Φ1830×7000 | 24 | 25 | ≤25 | 0.074-0.4 | 7.5-17 | 245 | 36 |
Φ2200×5500 | 21 | 30 | ≤25 | 0.074-0.4 | 10-22 | 370 | 48.5 |
Φ2200×6500 | 21 | 31 | ≤25 | 0.074-0.4 | 14-26 | 380 | 52.8 |
Φ2200×7500 | 21 | 33 | ≤25 | 0.074-0.4 | 16-29 | 380 | 56 |
Φ2400×7000 | 21 | 34.5 | ≤25 | 0.074-0.4 | 18-32 | 400 | 62.8 |
Φ2400×8000 | 20.4 | 36 | ≤25 | 0.06-0.08 | 18-36 | 410 | 81.2 |
Φ2700×3600 | 18 | 37 | ≤25 | <0.08 | 50 | 410 | 77.5 |