Belt Roasting Machine
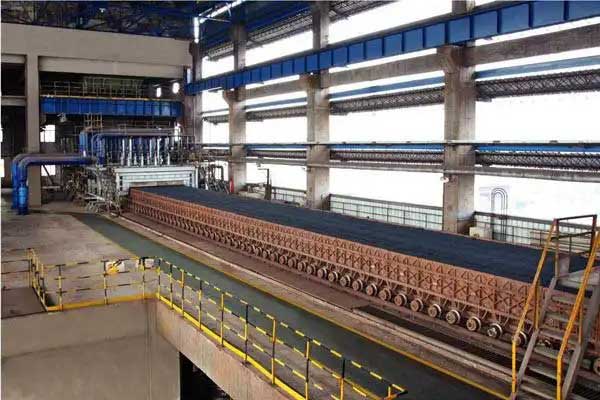
Belt Roasting Machine Introduction
The large-scale pellet belt roaster is a dynamic high-temperature equipment, and the key equipment includes a roasting system, a hot air system, and a combustion system. The structure of the equipment is complex, the working conditions vary greatly, and there are many factors that affect the application effect of refractory materials. There are high requirements for the performance, structural design and construction of refractory materials. The structural design, material configuration and masonry construction quality of refractory materials are the key to ensure A key factor in the efficient operation of equipment. The design of refractory materials needs to follow the design ideas of longevity, equalization, energy saving and functionalization, and comprehensively solve the problems existing in the application of refractory materials for key parts of large-scale belt roasting, so that the service life of refractory linings in various parts is balanced and downtime is reduced The frequency of maintenance can effectively extend the service life, improve the production rate, reduce energy consumption, and improve the overall efficiency of resources.
The belt roasting machine is especially suitable for expanding the production scale and realizing large-scale requirements. Its maximum has reached 750 square meters, and the output of a single machine has reached more than 5 million tons per year. In the 1980s, our company had trial-produced roasting trolleys for the roasting machines operated by Anshan Iron and Steel and Baotou Steel, and signed a supply contract for 388.5㎡ roasting machines with Middle East users in 2012, with a design capacity of 2.5 million tons per year. Achieved a breakthrough in the design and manufacture of domestic belt roasting equipment.
The belt roasting process was developed inspired by the belt sintering machine process. It is also a very mature pellet production process. In the past, it was restricted by conditions such as raw materials, fuels and equipment manufacturing materials. The domestic development is relatively slow. But it develops very fast. The entire process (drying, preheating, roasting, cooling) is completed on one device, which has the characteristics of simple process, compact layout, and light tonnage of required equipment. The recycling of gas and the reduction of heat and electricity consumption create conditions.
Roasting for various materials
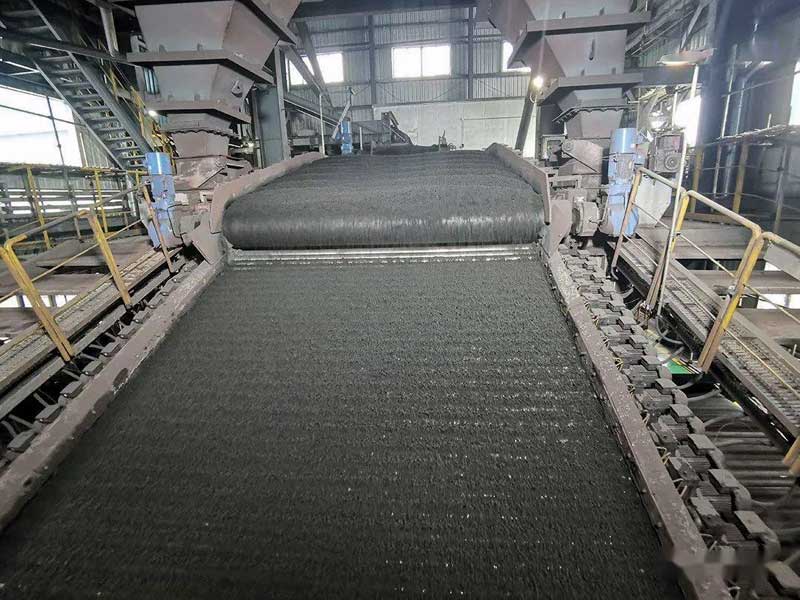
According to the nature of the material and the subsequent processing method, roasting has different purposes:
- Make the non-oxide minerals in the ore into oxides, these oxides will be transferred to the solution in the hydrometallurgical process to extract metals, and will be reduced to the metal state in the pyrometallurgical process;
- Remove moisture and other volatile components (such as arsenic, antimony, etc.) that are harmful to the metallurgical process in the ore:
- Make the powdery material into block or pellet, which is beneficial to the smelting process. Any type of roasting process is a multiphase chemical reaction process between solid and gas phases.
Roasting classification of Belt Roasting Machine
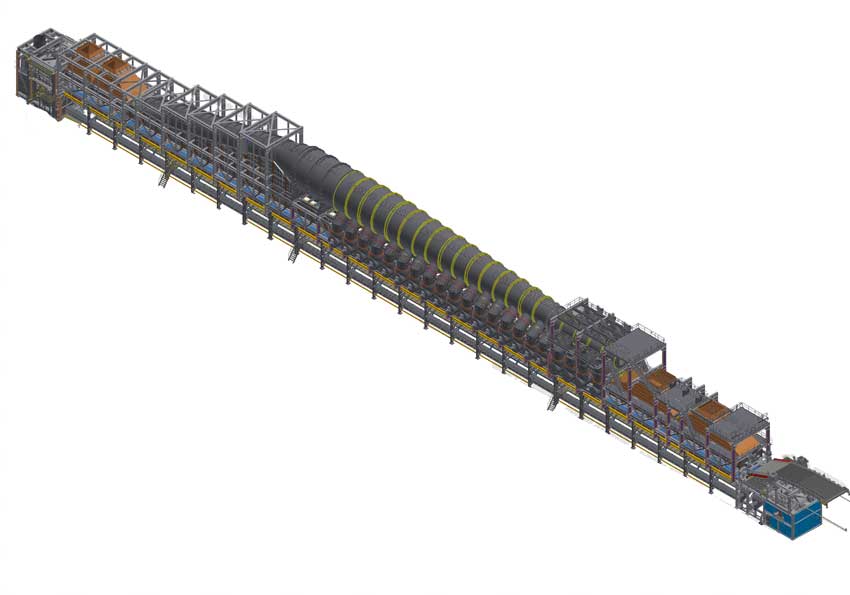
According to the purpose of the process, roasting can be roughly divided into: oxidation roasting, salinization roasting, reduction roasting, volatilization roasting, sintering roasting, among which salinization roasting includes sulfate roasting, chlorination roasting and soda roasting, and magnetization roasting belongs to reduction roasting. According to the movement state of the material in the smelting process, it can be divided into fixed bed roasting, moving bed roasting, fluidized roasting and floating roasting.
Belt Roasting: Machine Working Process
The roasting process of the large-scale pellet belt roaster includes drying, preheating, roasting, soaking, cooling and other processes, and each process is completed on the main equipment of the belt roaster. Different parts of the main equipment have relatively different performance requirements for refractory materials. It is necessary to develop new refractory functional materials with longevity, functionality and energy saving according to working conditions to achieve balanced, long-life, high-efficiency, energy-saving and environmentally friendly operation of equipment.
Roasting is the process of completing a certain chemical reaction below the melting temperature of the material, which is an integral part of the charge preparation. Most of the materials always exist in solid state, so the roasting temperature is limited to ensure that the materials do not melt significantly. Obviously, the roasting reaction is mainly solid-gas reaction, and sometimes there are solid-solid, solid-liquid and gas-liquid interactions or interactions. Roasting mostly prepares for the main smelting operations such as smelting or leaching in the next step, so it is often a charge preparation process in the smelting process, but sometimes it can also be used as a enrichment, impurity removal, metal powder preparation or refining process.
- The belt roaster is different from the belt sintering machine. The roasting of finely ground iron concentrate pellets and the sintering of iron powder are essentially different in the principle of consolidation, resulting in a great difference in industrial production technology. different. Therefore, it will be very complicated and difficult to transform a general sintering machine into a belt roasting machine. The belt roasting machine is very similar to the sintering machine in appearance, but there is a big difference in the equipment structure. For example, the structure of the trolley and the load bearing of the support, the distribution of the bellows and the sealing requirements. The setting and sealing of the upper furnace cover, the direction of the air flow (not a single draft like the sintering machine, but a combination of draft and drum Wind), the way of distributing materials, the discharge of finished products and the running speed of the trolley are all different, especially the material of the main body is completely different. In order to be able to safely withstand the temperature of the highest roasting gas (≥1300°C) for a long time, special alloy steel with excellent high temperature resistance has to be used. During the development of the belt burner in foreign countries, it was once frustrated because the material was unqualified, which made the grate-rotary kiln under development at the same time get a great development. Because the grate machine-rotary kiln process is to place the highest temperature section of the roasting process in a rotary kiln equipped with a refractory lining, this smoothly solves the material problem in high-temperature roasting. However, the belt roasting machine passed the test and achieved great development only after using the bottom pavement material and the trolley made of high-temperature-resistant alloy special steel.
-
Advantages of the belt roaster process
1) The entire process of pellet roasting—drying, preheating, roasting, and cooling—is completed on one device, which has the characteristics of simple process, compact layout, and light tonnage of required equipment. , It creates conditions for the factory to reduce the floor area, reduce the amount of engineering, realize the recycling of roasting gas, and reduce heat and power consumption.
2) It can adapt to the requirements of expanding production scale and realizing large-scale requirements. Its maximum has reached 750m2, and the output of a single machine has reached more than 5 million tons.
3) The adaptability to raw materials is stronger than that of the shaft furnace. This is because during the entire roasting process, the pellets are in the state of static material layer, and will not produce powder due to the change of the strength of the pellet itself (high and low) and the relative motion between the balls during the heating process. The conventional roasting process is basically suitable for all kinds of minerals.
4) Due to the reasonable setting of the thermal system and the short pipeline, in theory, the heat consumption of the belt roaster can reach the lowest level, and it has also created the best record in practice. -
Disadvantages of the belt burner
1) The high-grade special alloy steel with high temperature resistance is used in a large amount. Under the conditions of localization a month ago, it was quite difficult, especially in terms of quality.
2) In the production process, the stability requirements of raw materials are high. This is because the whole process of roasting (drying, preheating, roasting, cooling) is carried out on the same equipment, and it is impossible to change the residence time of pellets in each stage by adjusting the speed of the machine.
3) The quality of the finished pellets is uneven. As the temperature of the pellets rises, the length of residence time of the upper and lower material layers at the highest temperature of each section of the furnace cover is very different, which will affect the final strength of the finished pellets. In addition, the temperature in the furnace hood and the more or less edge effects on the trolley will also affect the quality of the finished pellets.
4) Gas and heavy oil with high calorific value must be used as fuel. The practice of using coal has not had long-term success in industry. Lurgi once studied a patented technology of coal injection and combustion in the upper wind hood, but it stopped after only one month of use in India's Demucred plant.
The belt roaster process is a very mature pellet production process, but it is also restricted by some conditions (such as raw materials, fuels and equipment manufacturing materials), so it needs to be taken very seriously when adopting this process.