Indirect Fired Rotary Kiln
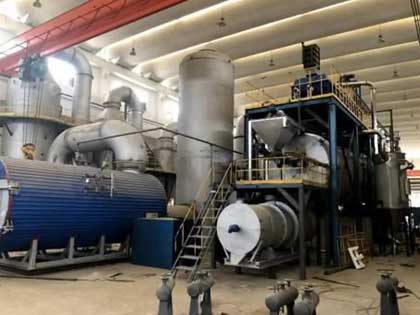
What is Indirect fired rotary kiln
External heated rotary kiln is a indirect fired thermal heating equipment widely used in building materials, metallurgy, chemical industry, non-ferrous metals and other industries. The material can be rolled and stirred along the tangential direction in the cylinder and moved along the axial direction.
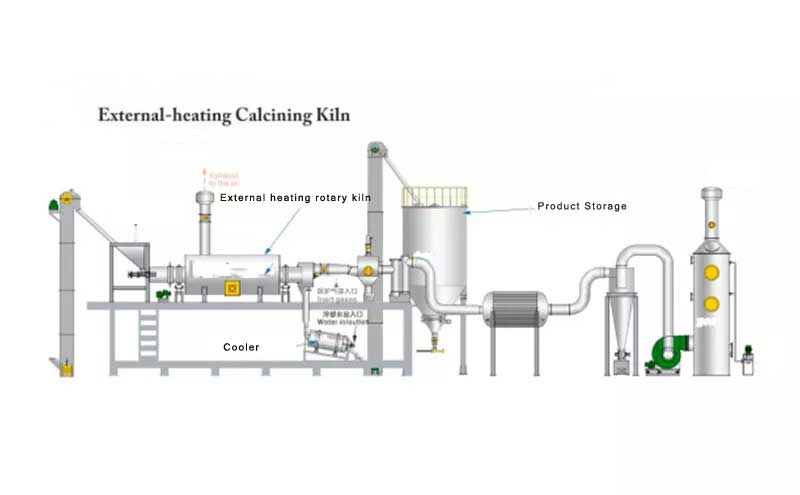
In the metallurgical industry, rotary kilns can be divided into internal heating rotary kilns and external heating rotary kilns according to different heating methods. The material of the indirect fired rotary kiln is not in direct contact with the flame and flue gas. The heat source is between the heating furnace and the cylinder, and the material is heated by heat transfer through the heat-resistant steel cylinder wall. The lining of the heating furnace is made of refractory fiber, which can save energy and reduce consumption. It is especially applicable when dealing with the requirements of high toxicity, high smoke concentration and high product purity.
The heating source of the high-temperature indirect heating rotary kiln is outside the furnace tube. The material is heated through the heat transfer to the furnace tube, so that the material in the furnace tube reaches the required calcination temperature, and the highest high-temperature atmosphere is 1200 ° C. This equipment is mainly used in pellets, Industrial scenarios such as high-temperature oxidation reaction, high-temperature reduction reaction, and chemical roasting where powdery raw materials cannot be directly heated.Indirect heating and calcination of catalysts, precious metals, electrodes, chemicals, new materials, powders, granular materials, etc.
Heating Source of Indirect Fired Rotary Kiln
There are various types of fuels available for external fired rotary kiln, it can utilize natural gas, fuel oil, electromagnetic heating, resistance heating, or silicon carbide rod heating, 3 main types of fuels are:
- Gaseous fuels such as coal gas and natural gas.
- Liquid fuels such as diesel and crude oil.
- Solid fuels such as coal and coke.
How to Utilize Different Types of Fuels
- Gas fuels for indirect fired rotary kilns, the choice depends on the specific production requirements. Different gas fuels require different nozzle structures and materials. To assess the fuel efficiency of the rotary kiln, factors such as complete combustion, flame length, flexibility in kiln temperature control, energy-saving effects, and maintenance efficiency need to be evaluated.
- Solid fuels like coal powder and coke powder are commonly used, but they can introduce pollution during combustion, which is difficult to eliminate during production and can adversely affect material yield during use. Therefore, it's advisable to avoid using lump coal or heavy oil as fuels for rotary kilns whenever possible.
- For liquid fuels, it's essential to control the fuel supply system or electric heaters for insulation effectively. Moreover, ensuring high-quality purity is crucial because oil pipes are prone to blockages. The use of low-quality oil can exacerbate blockages, thus impacting the normal operation of industrial rotary kilns. Therefore, maintaining a well-functioning fuel supply system, using high-quality fuel, and implementing proper insulation measures are necessary to ensure the smooth operation of rotary kilns in industrial settings.
Indirect Fired Rotary Kiln Features
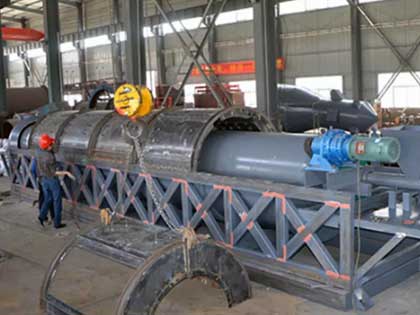
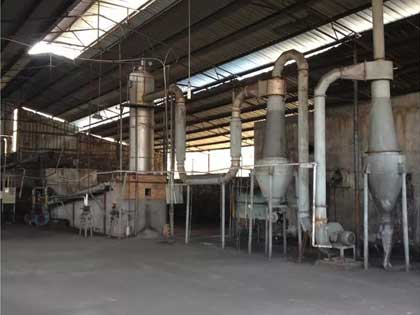
- High temperature 1200℃, externally heated rotary kiln High temperature externally heated rotary kiln adopts special high temperature resistant alloy material as the main material, matched with high temperature type heating element, can realize the maximum operating temperature of 1200℃.
- The rotary structure has a wide range of applications. The mature rotary kiln structure can not only be used for high-temperature oxidation (magnetic material iron oxide, cobalt oxide, manganese oxide, zinc oxide, molybdenum oxide, vanadium oxide, tungsten oxide) reaction, high-temperature reduction (manganese oxide oxidation Vanadium) reaction, chemical molecular sieve roasting and other industries, it is also compatible with the calcination or roasting of various granular or powder materials.
- The calcining time and process can be adjusted To adapt to large-scale continuous production. The heat source is controlled by imported SSR thyristor or power regulator, with high temperature control accuracy. At the same time, the working temperature can be adjusted according to the actual production process. The calcining time can be adjusted in various ways. Flexible and stable.
- Fewer wearing parts facilitate maintenance. The heating chamber adopts an upper and lower 2-stage assembly design, which is convenient for disassembly during maintenance. High-quality heating elements have a long service life. They are arranged in parallel, side-mounted, and drawer types, and are easy to replace. Less, it reflects AGICO careful efforts in humanized design.
- Structural optimization to reduce loss The equipment has compact structure, simple operation and maintenance. There is a heat preservation cover outside the heating furnace, and a heating chamber is formed between the cylinder and the cylinder, so that the cylinder is heated evenly and at the same time reduces heat loss. The tail end is supported by supporting rollers, with a large contact area, the thermal expansion can be released in time, and the damage to the cylinder body from internal stress can be reduced.
- High operating rate, energy saving and environmental protection By controlling the heat source, the use efficiency of the external heating rotary kiln will be higher. The working principle of the external heating rotary kiln is more convenient to clean, and it saves fuel, which helps to protect the environment and reduces damage caused by excessive heat. result in damage to the equipment.
Indirect Fired Heated Rotary Kiln Working Principle
The external heating system employs a heat source located outside the cylinder, utilizing gas flames, resistance wires, or electromagnetic heating. Direct heating of the cylinder wall ensures high heat transfer efficiency and minimal heat loss. The heating device is positioned within the insulation layer, where the generated heat from combustion or residual heat is utilized to heat the cylinder within the insulation layer, resulting in significant energy savings.
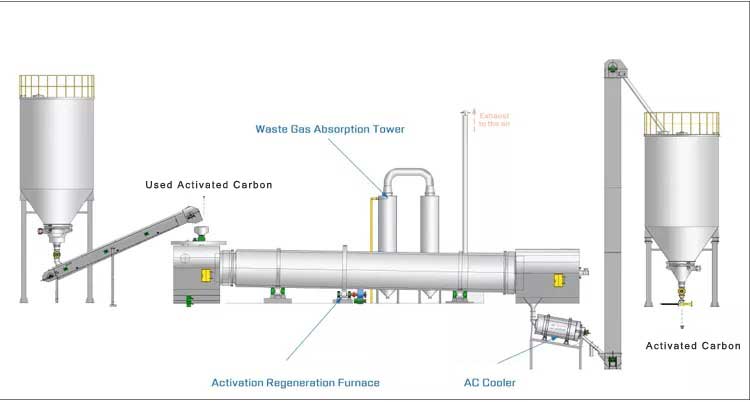
The material to be burned is evenly fed into the kiln barrel from the kiln head hopper through the feeding mechanism. Driven by the transmission device, the material advances along the axis of the barrel with the rotation of the barrel, and the lifting plate turns over the material to make it calcined evenly. . A heating chamber is provided outside the cylinder. The heat generated by calcination is transferred to the material through the cylinder, and the material is decomposed, dried, calcined and roasted at high temperature. The calcined material is discharged through the unloading valve, cooled and packaged for use.
Indirect Fired Rotary Kiln Technical Parameters
model | Specification | Designing ability | electric motor | reducer | weight | ||
(t/h) | model | power (kw) | model | speed ratio | (t) | ||
WY118 | Φ1.18×14 | According to material | YCT225-4A | 11 | ZS75-8-1 | 112 | 33 |
WY65 | Φ0.65×11 | According to material | YCT200-4B | 7.5 | ZS65-8-1 | 112 | 25.3 |
WY40 | Φ0.4×4.8 | According to material | YCT200-4A | 5.5 | ZS50-7-1 | 100 | 16 |
WY120 | Φ1.2×20 | According to material | YCT225-4A | 11 | ZS75-8-1 | 112 | 48 |
WY150 | Φ1.5×28 | According to material | YCT225-4B | 15 | ZS95-9-1 | 125 | 68 |
Internal heating rotary kiln
Internal heating rotary kiln is used for calcination of various materials, widely used in cement, chemical industry, metallurgy and other industries. Our company's professional team researches and designs and supports a number of patented technologies to create a professional brand in the industry.
Internal heating rotary kiln product description
In the metallurgical industry, rotary kilns can be divided into internal heating rotary kilns and external heating rotary kilns according to different heating methods. The material of the internal heating rotary kiln is in direct contact with the flame and flue gas, and the oxidation or reduction atmosphere in the furnace can be realized through adjustment. There is a flexible seal between the bodies, which can completely prevent dust and material leakage. Multi-level support can be adopted to make the cylinder length reach 60 meters, and the maximum operating temperature can reach 1600°C. The output is relatively large, and the applicable fuels are liquefied petroleum gas, natural gas, coal gas, fuel oil, pulverized coal, coal, etc.
Automatic control, energy saving and environmental protection
The supporting equipment has a high degree of mechanization, can be automatically controlled, has good roasting quality, large output, long service life of equipment, saves energy and facilitates environmental management.
Convenient heating and quality controllable
Different combustion devices can be used for various fuels to provide heat for the rotary kiln, and the tail gas treatment system can recycle materials. Rotary kiln occupies an important position in some ferrous and non-ferrous metals. This equipment is used for heat treatment such as sintering and roasting of ores, concentrates and intermediate products. Chemically change the material to produce materials that meet the requirements.