Jaw Crusher
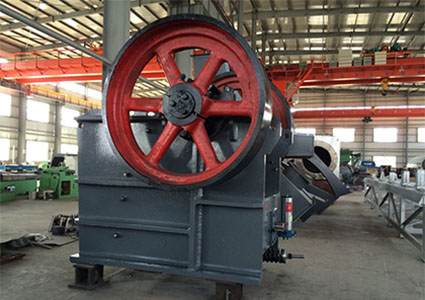
- Applications: Widely used in mining, cement and concrete industries. Mainly used as coarse crusher and medium crusher in mining, building materials, infrastructure and other departments.
- Processing Materials: widely used in river pebble, rock (limestone, granite, basalt, diabase, andesite, etc.), ore tailings, stone chips, building aggregates, road road fabrics, cushion materials, asphalt concrete and cement concrete aggregates Fine and coarse grinding operations, machined sand production and stone shaping in the engineering field.
- Equipment Types: PE series, PEX series.
Jaw Crusher Introduction:
Jaw crusher applies to the various minerals or rocks with strongest anti-crush pressure less than 250Mpa. It is widely used in mining industry, cement production line and concrete industry. and mainly used to be boulder crusher and middle crusher in the mining, building materials, capital construction or any other fields.
Case Sample:
The main processing material- iron ore of the PE600×900 jaw crusher provided by AGICO for Iron Selection plant. The feed size is 500mm. The discharge size is 75-200mm, and the output is 60-200t/h. 75kw. It is used to provide rough grinding of the raw materials for the ball mill. The PE600×900 jaw crusher is suitable for limestone crushing. Jaw Crusher supplied for those projects have been used for more than 5 years.
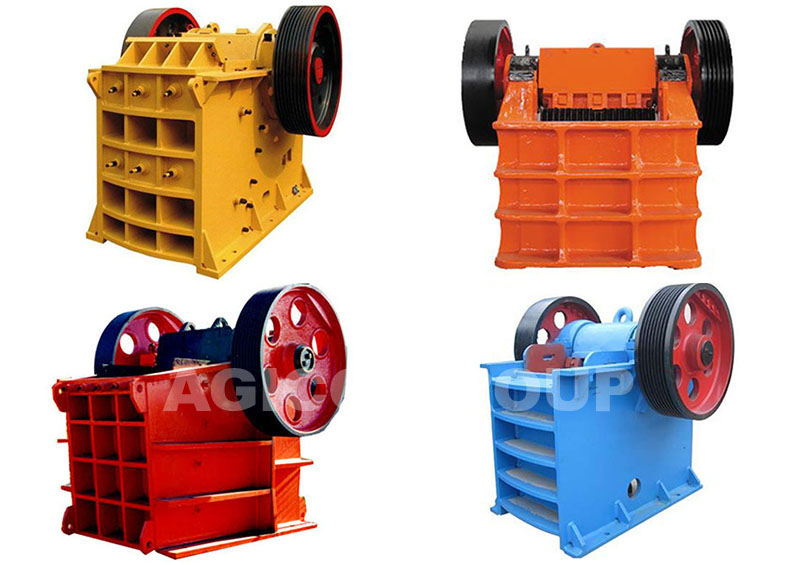
The jaw crusher is widely used in the first processing of various rock crushing. In view of the fact that the customer's processed materials are hard granite, it has high abrasion resistance and high wear resistance. We recommend PE series large jaw crusher PE900---PE900×1200 as the first crushing process to reduce the cost of hard rock crushing.
Structure of Jaw Crusher
The working part of the jaw crusher is 2 jaws, one is a fixed jaw (fixed), the vertical (or the upper end is slightly inclined) fixed on the front wall of the body, and the other is the movable jaw (moving), the position Tilting, forming a large and small crushing cavity (working cavity) with the fixed jaw. The movable jaws periodically reciprocate against the fixed jaws, sometimes separated and sometimes closed. When separated, the material enters the crushing chamber, and the finished product is discharged from the lower portion; when it is close, the material between the two jaws is crushed by bending, bending and splitting.
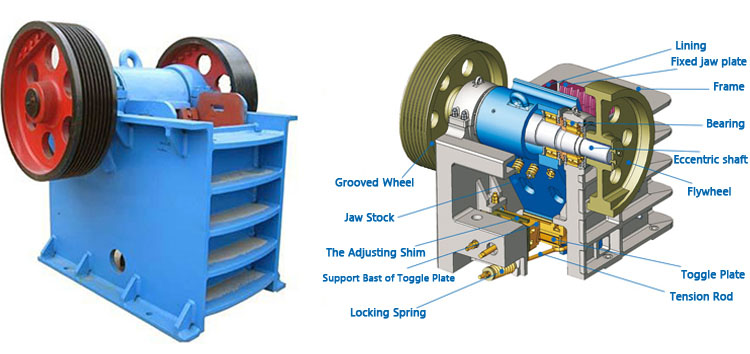
The jaw crusher can be divided into a simple swing jaw crusher (simplified pendulum jaw crusher) according to the different swinging modes of the movable jaw. There are 3 kinds of complex swing jaw crusher, complex pendulum jaw crusher and integrated swing jaw crusher.
PE Serie Jaw Crusher Technical Parameter:
Mode |
Feed Opening Size(mm) |
Maximum feed length(mm) |
Adjustable Range of Output Size((mm) |
Capacity(t/h) | Motor Power (kw) | Weight(t) |
Overall Dimension(mm) |
---|---|---|---|---|---|---|---|
AG PE250×400 | 250×400 | 200 | 20-50 | 5-20 | 15 | 2.9 | 1430×1310×1340 |
AG PE400×600 | 400×600 | 350 | 40-100 | 15-60 | 30-37 | 6.8 | 1700×1732×1653 |
AG PE500×750 | 500×750 | 425 | 50-100 | 40-100 | 45-55 | 11.2 | 2035×1921×2000 |
AG PE600×900 | 600×900 | 480 | 65-160 | 60-140 | 55-75 | 16.5 | 2290×2206×2370 |
AG PE750×1060 | 750×1060 | 630 | 80-150 | 80-230 | 90-110 | 29 | 2655×2302×3110 |
AG PE900×1200 | 900×1200 | 750 | 95-165 | 140-320 | 110-132 | 54.5 | 3789×3050×3025 |
AG PE1000×1200 | 1000×1200 | 850 | 105-185 | 180-400 | 160-200 | 56.5 | 3900×3320×3280 |
AG PE1200×1500 | 1200×1500 | 1020 | 150-300 | 250-650 | 220-250 | 99.6 | 4300×3540×4043 |
PEX Serie Jaw Crusher Technical Parameter:
Mode |
Feed Size (mm) |
Maximum feed length (mm) |
Adjustable Range of Output Size (mm) |
Capacity (t/h) |
Motor Power (kw) |
Weight (t) |
Overall Dimension (mm) |
---|---|---|---|---|---|---|---|
AG PEX150×250 | 150×250 | 125 | 10-40 | 1-3 | 5.5 | 0.85 | 896×745×935 |
AG PEX150×750 | 150×750 | 125 | 12-45 | 5-16 | 15 | 3.8 | 1205×1495×1203 |
AG PEX250×750 | 250×750 | 210 | 25-60 | 10-40 | 22-30 | 5 | 1667×1545×1020 |
AG PEX250×1000 | 250×1000 | 210 | 25-60 | 15-50 | 30-37 | 6.8 | 1964×1550×1380 |
AG PEX250×1200 | 250×1200 | 210 | 25-60 | 20-60 | 37-45 | 8.5 | 2192×1605×1415 |
AG PEX400×1200 | 400×1200 | 320 | 35-95 | 28-95 | 45-55 | 11.7 | 2256×2100×1960 |
Jaw Crusher Equipment Performance
-
Adopt World-class Manufacturing Technology
the highest-end materials are used. For example, the dynamic boring assembly is made of high-quality steel castings, and the heavy-duty eccentric shaft is processed by forging blanks, which makes the equipment extremely reliable and durable. -
Higher Strength
Using finite element analysis technology, the integral cast steel bearing seat ensures complete cooperation with the frame, which greatly enhances the radial strength of the bearing housing and enables the equipment to have higher strength. -
Safe and Fast Adjustment
The crushing chamber adopts a symmetrical "V" shape structure, and the discharge opening adopts a wedge adjusting device, and the adjustment is simpler, safer and faster. -
Larger Carrying Capacity
With larger and more durable eccentric shaft bearings and toothed guards provide greater load carrying capacity, higher output and longer service life.
Jaw Crusher Working Principle
The upper end of the movable cymbal is directly suspended on the eccentric shaft, and the connecting rod as the crank connecting rod mechanism is directly driven by the eccentricity of the eccentric shaft. lower end of the movable cymbal is hinged to the thrust plate and supported on the rear wall of the frame. When the eccentric shaft rotates, the trajectory of each point on the moving cymbal is from the circumferential line of the suspension point (the radius is equal to the eccentricity), and gradually becomes elliptical downward. The lower the part, the more the ellipse is biased until the lower part and the thrust plate The connection point track is a circular line. Because the movement trajectory of each point on the moving cymbal is complicated, it is called a complex oscillating jaw crusher.
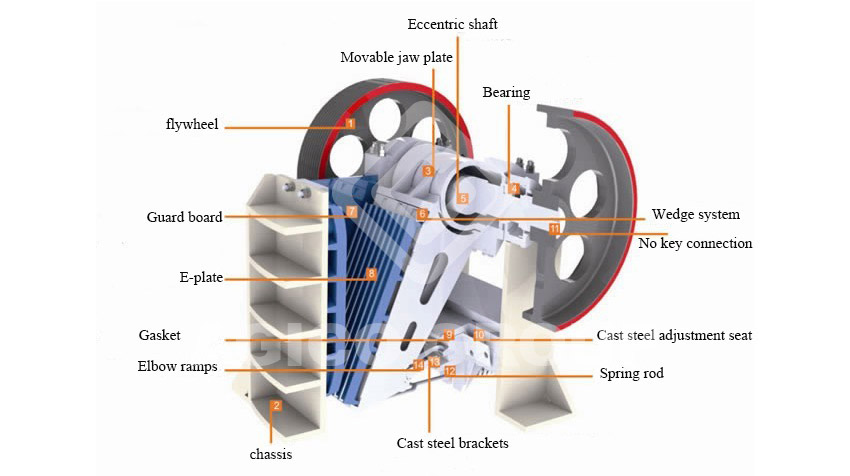
When the jaw crusher is in operation, the movable jaws periodically reciprocate the fixed jaws, sometimes approaching and sometimes away. When approaching, the material is crushed by crushing, splitting, and impact between the two jaws; when leaving, the material that has been broken is discharged from the discharge port by gravity. When feeding the jaw crusher, the material is poured from the top inlet into the crushing chamber containing the molars, which force the material to the wall of the chamber and break it into smaller stones. Supporting the movement of the caries is an eccentric shaft that runs through the fuselage frame. The eccentric motion is generated by a pulley driven by a pulley fixed to the shaft end through a motor, and the flywheel at the other end of the shaft acts as a balance. Pulleys, flywheels and eccentric shaft support bearings often use spherical roller bearings, which must withstand large shock loads, abrasive sewage and high temperatures.