Rotary Cooler
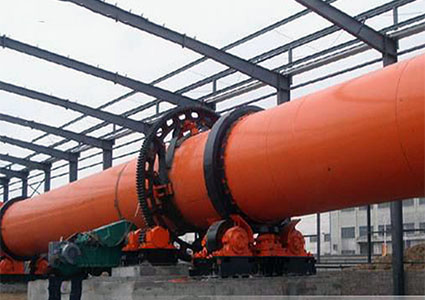
- Applications: Cement, building materials, mining, metallurgical and other industries
- Materials: limestone, cement clinker, bauxite, activated lime, aluminum hydroxide, etc.
- Rotary Cooler Models: Y160L-6, Y200L1-6, Y225M-6, Y280S-6, Y280M1-6, YS2-355M1-6
Rotary Cooler Description:
The Rotary Cooler is often used to cool the kiln clinker of the 500-2000t/d production line because of its simple structure, high thermal efficiency, low maintenance cost, low equipment investment and high operating efficiency. It is also very important that the rotary cooler is an indispensable cooling device in the process of calcining the material in the rotary kiln. Mainly composed of reducer, hot air duct, furnace body, cooling water, feed chute, lifting plate, discharge part, front and rear roller ring, cylinder, motor and other structures.
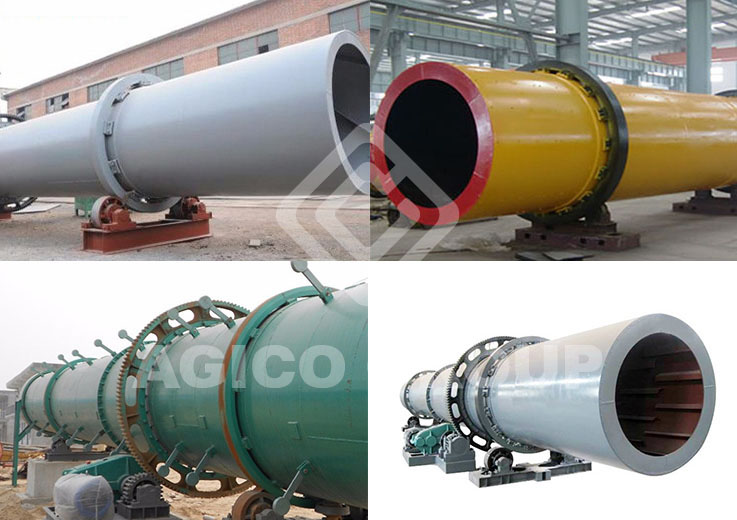
AGICO can also configure feeders, conveyors and other related equipment according to requirements of users. The main function of Rotary cooler is to cool material by air cooling from the high-temperature material, and recover the heat in the exhaust gas as the secondary and tertiary air of the rotary kiln, thereby improving thermal efficiency of rotary kiln.
Suited Materials
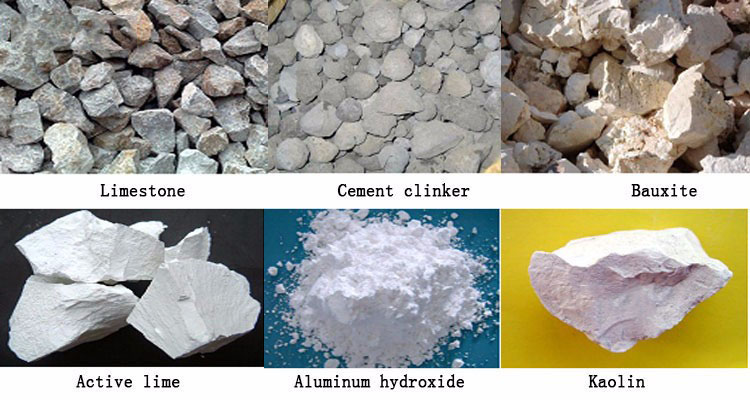
Technical Parameter
Model | Production Capacity (t/h) | Rotation Speed (r/min) | Motor Model | Power(kw) | Reducer | Total Weight (t) |
---|---|---|---|---|---|---|
Φ1.2xl2 | 1.9-2.5 | 4.5 | Y160L-6 | 11 | ZQ50 | 22 |
Φl.5xl5 | 4-6 | 4.5 | Y200L1-6 | 18.5 | ZQ65 | 33 |
Φ2x20 | 7-8 | 3 | Y225M-6 | 30 | ZL75 | 74 |
Φ2.2x22 | 10-11.5 | 3 | Y225M-6 | 30 | ZL75 | 82 |
Φ2.5x25 | 11-15 | 3.5 | Y280S-6 | 45 | ZL100 | 108 |
Φ2.8x28 | 14-17 | 3.5 | Y280M1-6 | 55 | ZL100 | 142 |
Φ3x30 | 16-20 | 3.5 | YS2-355M1-6 | 112 | ZL115 | 156 |
Rotary Cooler Structure and Features:
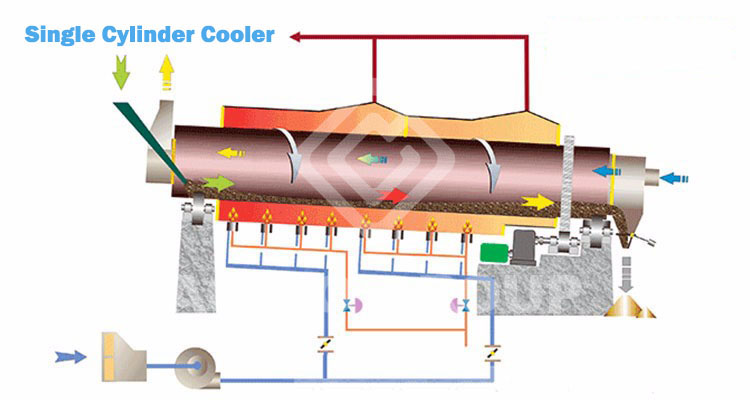
Rotary Cooler is mainly composed of reducer, hot air duct, furnace body, cooling water, feed chute, lifting plate, discharge part, front and rear roller ring, cylinder, motor and other structures Performance characteristics: The rotary cooler is one of the important equipments in the rotary kiln system and has the following characteristics: First, the clinker from the rotary kiln (1000-1200 °C) through the cylinder rotating belt animal material and air for full heat exchange, so that the material is cooled to (below 200 ° C), while improving the quality of clinker and easy to wear, Second, the air after cooling the material is all put into the kiln, as the secondary circulation air, the thermal efficiency of the kiln is improved. Third, the structure is simple, the operation rate is high, and the operation and maintenance are convenient.
Working Principle of Rotary Cooler:
The dried wet material is sent to the hopper by belt conveyor or bucket elevator, and then fed through the hopper through feeding pipe into feeding end. The slope of feeding pipe is greater than natural inclination of material so that material flows smoothly into the cooler. The cooler cylinder is a rotating cylinder that is slightly inclined to horizontal. Raw material is added from the higher end, heat carrier is discharged from the lower end, and is in countercurrent contact with raw material, and heat carrier and the material are simultaneously flowed into the cylinder.
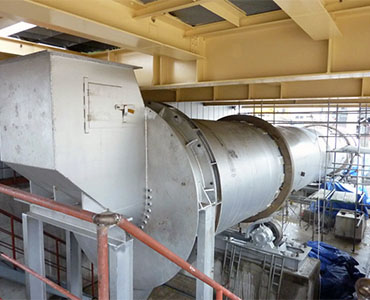
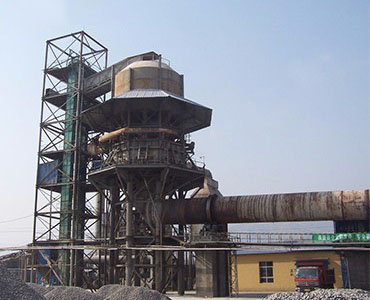
As the rotating material of cooler cylinder is moved by gravity to the lower end. During forward movement of the wet material in the cylinder body, the heat supply of the heat carrier is directly or indirectly obtained, so that hot material is cooled, and then sent out at the discharge end through a belt conveyor or a screw conveyor. A copy board is arranged on the inner wall of cylinder, its function is to copy and sprinkle the material, so that the contact surface of material and the air flow is increased to increase cooling rate, promote the advancement of the material. The cooling body is generally classified into cold air. After the heat carrier passes through the cooler, a cyclone is generally required to trap the material contained in the gas. If you aim to further reduce the dust content of the exhaust gas, you should also discharge it after passing the bag filter or the wet dust collector.