Instructions for Preparation of Clinker Production Plant Test Running
The Qingzhou 6000T/D Cement clinker production project of Zhonglian Cement Co., Ltd. mainly includes the following 4 systems:
- Raw material grinding and waste gas treatment system: including limestone crushing and transportation, limestone storage and transportation, auxiliary raw material crushing, transportation and storage, raw material batching station and transportation, fly ash storage and transportation, raw material grinding and waste gas treatment, raw material homogenization warehouse (the top part of the warehouse) and other projects.
- Raw material homogenization and kiln system: including raw material homogenization warehouse and raw material kiln two projects.
- Firing system: including firing kiln tail, firing kiln, firing kiln head, clinker storage and transportation, firing oil pump room and other projects.
- Pulverized coal preparation and measurement conveying system: including raw coal storage and conveying, pulverized coal preparation and conveying two projects. The debugging operation instructions will be described respectively according to the above system.
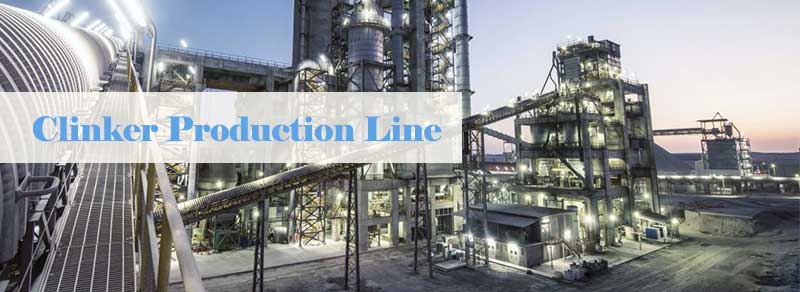
This debugging operation manual is based on the introduction of design of each process, such as process flow, selected equipment, electrical and process control, etc., according to its requirements and characteristics, in order to ensure the normal operation and production. Operators in a comprehensive understanding of this manual operation essentials, and at the same time, must also be familiar with every piece of equipment performance in the clinker production line, safe operation and maintenance methods and requirements, must be familiar with ipc methods and operation steps, and the range of normal work the point indicator and emergency alarm and how to deal with abnormal situations when it happens, so that in the actual production operation, timely operation will be taken to solve specific problems that may occur at any time, and sometimes the treatment can be flexible according to actrual situation. If you need info of performance, maintenance and operation methods and requirements of each equipment in the system, please refer to the single machine operation manual provided by each corresponding equipment supplier.
Preparation for Clinker Production Line Debugging Operation
After each equipment is being installed and connected, the whole clinker production plant is completed. Before the test running of clinker production line, each equipment must be checked against installation instructions provided by each equipment supplier, so as to verify whether it meets the installation requirements or not. After passing the inspection, a single no-load test operation can be carried out, which is also in the work list of equipment installation and acceptance. Before the no-load test run of certain equipment, the following tasks must be done:
Cleanup Surrounding of Clinker Production Equipment
Remove the sundries in and around clinker production equipments that have nothing to do with operation, especially the welding electrode tips, welding slag, refractory pieces, installation and testing tools, useless gaskets, steel plates and wood blocks left in the equipment during the installation process; Remove garbage and sundries on the stairs to ensure smooth and safe passage;
Remove the dust inside the dust collector; Drain the pit of water. Clean all floors of each workshop.
Check Clinker Production Line Installation | |
---|---|
Equipment Base and Connection Bolt | If it is tightened, the conditions of foundation welding parts, some stairs, aisle handrail bar has been welded as required or not; |
Measuring Point | Check it with the instrument, the installation position is suitable or not; |
Safety Cover or Safety Warning Sign | Equipment(such as belt transmission device, mill barrel, etc.) has been installed around the equipment; |
Lubrication Point Conditions | If each lubrication point of the equipment has been add enough lubricating oil (agent), the quality of oil is able to meet the requirements. If lubricating oil inside reducer has deteriorated, replace it with new oil; |
Cooling Water Pipe, Compressed Air Pipeline | Check to see if it is unblocked, whether there is leakage, the water pressure, air pressure is normal or not, has the oil pipe in the lubricating oil station been cleaned, and if there is pipeline oil leakage; |
Equipment Installation Precision | Make sure it can meet the requirements of the installation specification, whether the pipe flange connection surface is flat, there is no leakage seam (hole), each view, check whether the hole is sealed; After the installation of hot air duct, whether the fixed screw bolts of the expansion joint have been loosened; |
Equipment Steering | whether the equipment steering meets the requirements by inching, the circuit wiring, and the motor or special equipment has been correctly grounded as required. |
Manhole Doors, Manhole, Mill Doors | Check to see if it is closed |
Check Clinker Production Line Installation Details
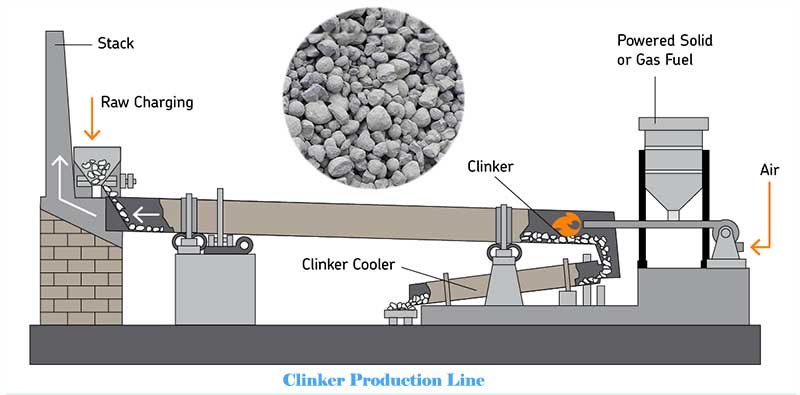
- Check whether the equipment base and connection bolts have been tightened, the conditions of foundation welding parts, some stairs, aisle handrail bar has been welded as required or not;
- Check the process measuring point with the instrument, the installation position is suitable or not;
- Whether safety cover or safety warning sign (such as belt transmission device, mill barrel, etc.) has been installed around the equipment;
- If each lubrication point of the equipment has been add enough lubricating oil (agent), the quality of oil is able to meet the requirements. If lubricating oil inside reducer has deteriorated, replace it with new oil;
- Check each cooling water pipe, compressed air pipeline to see if it is unblocked, whether there is leakage, the water pressure, air pressure is normal or not, has the oil pipe in the lubricating oil station been cleaned, and if there is pipeline oil leakage;
- Check equipment installation precision size, make sure it can meet the requirements of the installation specification, whether the pipe flange connection surface is flat, there is no leakage seam (hole), each view, check whether the hole is sealed; After the installation of hot air duct, whether the fixed screw bolts of the expansion joint have been loosened;
- Check whether the equipment steering meets the requirements by inching, the circuit wiring, and the motor or special equipment has been correctly grounded as required.
- Check whether the manhole doors, manhole, mill doors, etc, have been closed.
Check Wiring of Clinker Production Line
After the cleaning and inspection work has been completed one by one, the electrical control system wiring is checked, especially the motor power line wiring; Confirm that the alarm at each measuring point of the clinker production line is effective and the instruments and switches are intact; Confirm that the communication between the central control room and relevant workshops is normal, all safety measures have been implemented, and the maintenance tools are ready. After that, it can carry out no-load test operation. The single no-load test run generally takes about 4~8 hours. During the test run, the on-site debugging operators must stick to their position, pay close attention to the running of each clinker production equipment, find and solve problems timely, and record all found problems and solutions for maintenance.
Clinker Production Line is an important part of Cement plant project, if you need details or price of Clinker Production Line Equipments, feel free to contact us now!