Important Operation Tips For Cement Vertical Mill
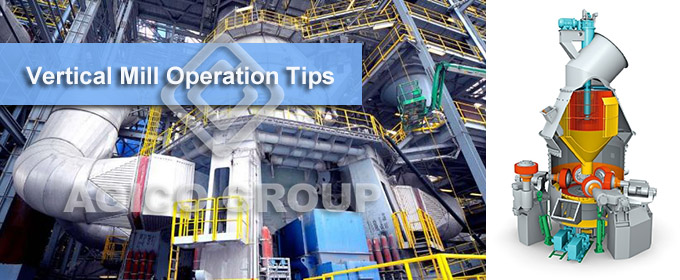
Regardless of Rotary kiln operation or grinding, it is necessary to clarify the inherent logical relationship of the system, which requires the operator to have a clear understanding of the characteristics of the system process and equipment. fully understand the dialectical relationship between qualitative and quantitative.
Operator must first learn about the operation of the system. Which equipment has hidden dangers, and how does production influence on cement quality. Read the full analysis report sheet to understand the material's grindability so that targeted control can be achieved. It is necessary to familiarize yourself with the operation interface of the central control and know the field equipment very well, so you should always go to the site to understand the situation of the equipment. Especially when the field device fails, you need to know the cause of the failure and the method to solve the problem.
Vertical mill is a equipment that grinds materials by relative rolling of a grinding roller on grinding disc. There are several aspects to the normal operation of the vertical mill:
The material layer of Vertical mill
The proper thickness of the layer and stable layer are basis for stable operation. The material layer is too thick will lead to grinding efficiency reduction, and when pressure difference of the mill reaches the limit, the material will collapse, which will affect main motor and venting system; If material layer is too thin, with driving force of the mill increases, the grinding roller, disc and hydraulic system are damaged.
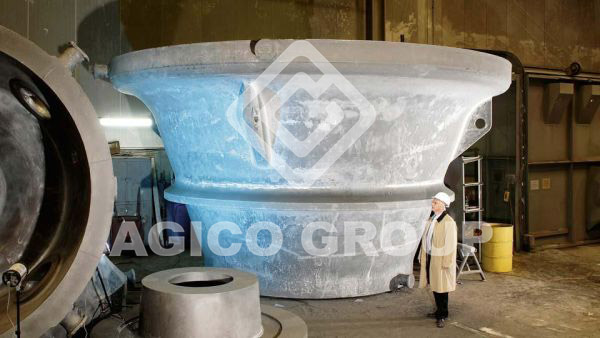
Vibration of Vertical Mill
Vibration Might Case Damages:
Excessive vibration of the vertical mill not only directly causes mechanical damage, but also affects production and quality. The factors that cause vibration are: the basis of the mill, the grinding pressure, the thickness of the layer, the air volume and the air temperature, the accumulator pressure, the wear of the roller surface or the grinding disc, and the like.
The influence of materials on vertical mill vibration and the treatment method: it is mainly reflected in the particle size, the wearability and the moisture. In the vertical grinding operation process, to form a stable material layer, it is required that the grinding material has a suitable gradation, and more than 95% of the particle size is less than 3% of the roller diameter. Excessive feed size will result in poor grindability. Since the gap between the bulk materials is not filled with enough fine particulate material, the buffering performance of the material bed is poor, and the impact force when the material is crushed is difficult to absorb, resulting in an increase in vibration. The feed size is too small, especially when the powdery material is long, because the small particle material has small friction and good fluidity. The lack of large materials constitutes a supporting skeleton, and it is difficult to form a stable material bed. The grinding roller can not be effectively pressed and crushed. A large amount of powdery material will increase the dust concentration and ventilation resistance in the airflow. When the limit is reached, the material will collapse and mill vibration will increase.
Material Grindability
When the material is too fine, especially when the internal pressure difference of the vertical mill has risen significantly, the feeding should be adjusted in time, grinding pressure and outlet temperature should be reduced and the water spray amount should be increased, powder separator speed should be appropriately reduced. The grinding pressure is increased under the premise of ensuring stable pressure difference and layer thickness.
Material grindability is an important factor affecting the yield. When material grindability deteriorates, grinding cycles number of vertical mill increases significantly. Since most of the material is crushed into fine powder, but it can not meet the requirements of the finished product, it cannot be taken out of the mill by the airflow. As the fine particle material on the grinding disc increases, there will be a situation similar to the fineness of the feed size. Vertical grinding pressure The difference is increased, the ventilation is not smooth, and the external circulation and internal circulation are greatly increased. At this time, the material layer will become extremely unstable, the load of the powder separator will increase, the thickness of the material layer will increase, and the load of the mill will increase. If it is not treated in time, the vibration of the vertical mill will be further aggravated and the main motor will be overcurrent.
Material Moisture
The influence of material moisture on the vibration of the mill can not be ignored. If the moisture content of the material is too low, it is difficult for the dried material to reliably form a stable bed on the grinding disc, which inevitably causes the mill to vibrate. When the moisture is too high and the layer on the grinding disc is too low, it is easy to form a cake, which increases the vibration of the mill. For example, in order to meet the material drying requirements, it is necessary to provide a larger air volume and a higher air temperature, which will make the wind speed in the mill higher, and the material that should be settled and dropped is forced to suspend, the external circulation is reduced and the internal circulation is increased. At the same time, due to the high adhesion of the high moisture material, the thickness of the upper layer of the grinding disc is thickened, which increases the chance of collapse and the balance of the bed.
The accumulator mainly provides cushioning for the lifting of the roller set. If the pressure of the accumulator is too high or the nitrogen balloon is broken, the buffering effect will be reduced or even completely lost, resulting in a hard impact of the grinding roller group and the material bed causing severe vibration of the mill.
Vertical Grinding Water Spray System
The vertical grinding water spray system plays an important role in stabilizing the material bed, especially in the case of more powdery materials or low water content in the raw materials, the effect is more obvious, the toughness and rigidity of the material can be increased, and the material grinding is facilitated, protect the roller surface and the grinding disc. The height of the retaining ring determines the maximum thickness of material bed. When the retaining ring is too low, the material layer as the cushion is thinned, the buffering effect is weakened, and the grinding machine will vibrate, and the high ring will cause grinding. Reduced efficiency, reduced production and increased electricity consumption. Excessive wear of the scraper plate, uneven wear of the guide vane and the wind deflector will cause uneven distribution of the air volume in the wind ring and the mill, resulting in different thickness of the material on the grinding disc, causing vibration. Excessive or too low temperature in the mill can lead to damage to the stability of the layer, especially when the temperature is too high, the material on the disc becomes very loose and easy to flow. Not only the material layer is thinned, but also it is not easily crushed by the grinding roller, causing vibration. If the temperature is too low, the material has poor fluidity and is easy to accumulate on the grinding disc, which will result in thickening of the material layer and a decrease in grinding efficiency.
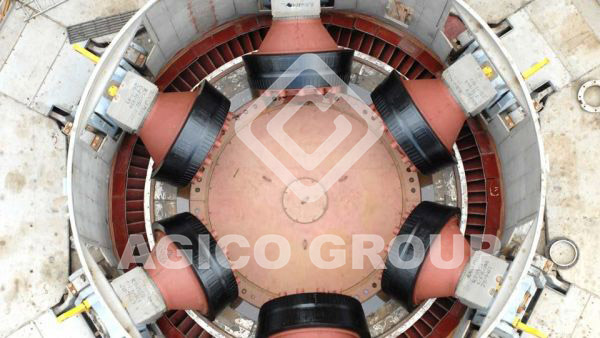
Grinding Pressure
Grinding pressure is the main factor affecting the quality of production. The grinding pressure is adjusted according to the amount of grinding machine feed, material size and easy grinding. In order to maintain a layer of material with a certain thickness on the grinding disc, reduce the vibration of the mill and ensure stable operation, the pressure of the grinding roller must be controlled. When the grinding pressure is increased, the grinding capacity of the mill is increased, but after reaching a certain critical point, it does not change. If the hydraulic cylinder setting pressure is too high, it will only increase the driving force and accelerate the wear of the components, and will not improve the grinding ability. This feature is similar to the working principle of a roller press. However, some manufacturers reduce the maximum value of the grinding pressure when setting the maximum grinding pressure, taking into account the protection equipment. When the grinding pressure is low, the thickness of the layer increases, the current of the main motor increases, the pressure difference within the mill increases, and the vibration of the mill increases. When the grinding pressure is high, the thickness of the layer decreases and the current of the main motor increases. The vibration speed of the mill increases and the component damage is accelerated. So maintaining a proper grinding pressure is a critical operation.
Mill Outlet Gas Temperature
When the temperature of the outlet gas of the mill is too low, the fluidity of the material will be deteriorated, and the qualified finished product cannot be extracted in time. When the pressure difference in the mill is too high, the material will collapse. The method of raising the temperature includes: increasing the suction of the mill, adjusting the fineness by the classifier; increasing the opening of the hot damper to reduce the opening of the circulating wind. These methods are also applicable to other types of raw material mills. However, if the temperature is too high (above 130 ° C), it will also cause damage to the equipment. The dividing wheel in the lower part of the cyclone will expand and become stuck, and the lubricating grease of the grinding roller will also be cracked. It is also disadvantageous for the tail dust bag. If there is too much powder on the grinding disc, the thickness of the layer will be unstable, so it is necessary to control the outlet temperature of the mill. Each mill has its own adaptation temperature, and the operator must master it during operation. For safety reasons, it is best not to close the inlet damper into the humidification tower during production.
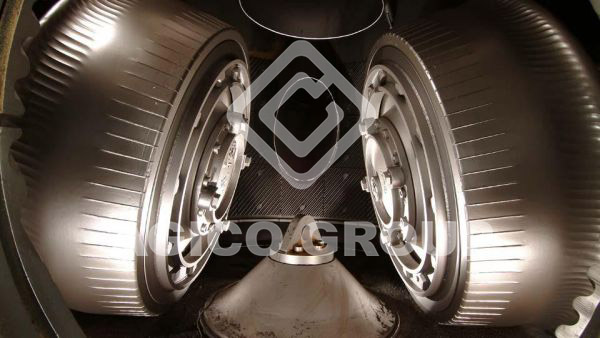
System Air Volume
The system air volume must be matched with the feeding amount. The method of adjusting the air volume can generally be controlled by adjusting the power of the mill circulating fan or adjusting the opening degree of the kiln exhaust fan. The wind is going big. When the system air volume is too large, the internal pressure difference decreases, the main motor current decreases; the thickness of the material layer is too low, the vibration value is large, and the sieve residue increases. When the system air volume is too small, the thickness of the material layer increases, the internal pressure difference increases, the main motor current increases, and the vibration of the mill increases.
The Amount of Slag Excessive
Feeding is large and satiety is a major cause. However, when the material is poor in wearability, it will also slag. The size of the grinding material is large, the system air volume is insufficient, the grinding pressure is low, the system leaks air, the material layer is unstable, the material ring is low, and the roller surface or the grinding disc wears seriously, which will cause the grinding machine to slag more.
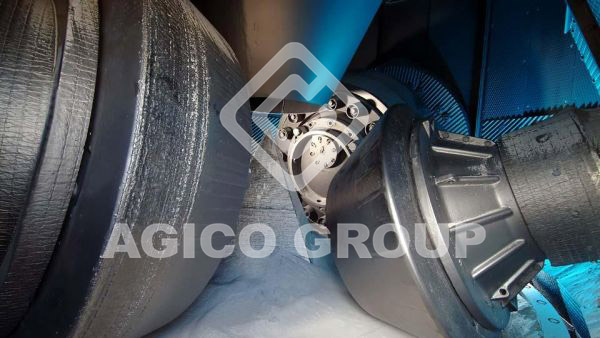
Mill System Operate Safety
When the raw material is running in the vertical mill, the drying heat source of the material comes from the hot gas at the kiln tail. Therefore, when the vertical mill is operated, the control of the inlet and outlet dampers should be balanced by the kiln mill. When the vertical mill inlet and outlet dampers are balanced, the system's wind will be balanced and will not affect the pressure at the kiln end.
Precautions for Starting and Stopping
Before the grinding starts, it is necessary to stack enough material on the grinding disc so that when the grinding roller falls and grinds, it will not stop due to high vibration. However, the material layer should not be too high, otherwise the main motor current will be high when the roll is ground, which is unfavorable to the equipment. The air pressure at the nozzle ring before grinding is a key value for the observation level. The situation of each vertical mill is different, and it must be reasonably controlled according to circumstances. Try to increase the ventilation before stopping the machine to make the fine powder into the reservoir as much as possible. If the fine powder is excessively rolled, the vibration of the mill is large.