How to Improve Cement Plant Process for Better Cement Quality
The cement quality control of cement plant is mainly based on specific technological process, which includes the quality control of various raw materials, semi-finished products used in the production process, the sampling analysis of materials, to ensure the stability and uniformity of raw material composition. The quality control of raw materials requires chemical composition analysis, to avoid the use of raw materials with large fluctuations. Raw material quality control includes chemical composition control and particle size water control, to ensure the uniformity and stability of the composition. The clinker needs to be chemically analyzed and physical properties checked, for guarantee of quality standards. All aspects of the quality control process need to be checked, to ensure the quality of finished cement. Aiming at the operation status and existing problems of original clinker grinding unit of a cement plant, the overall reconstruction scheme, management methods and implementation were formulated.
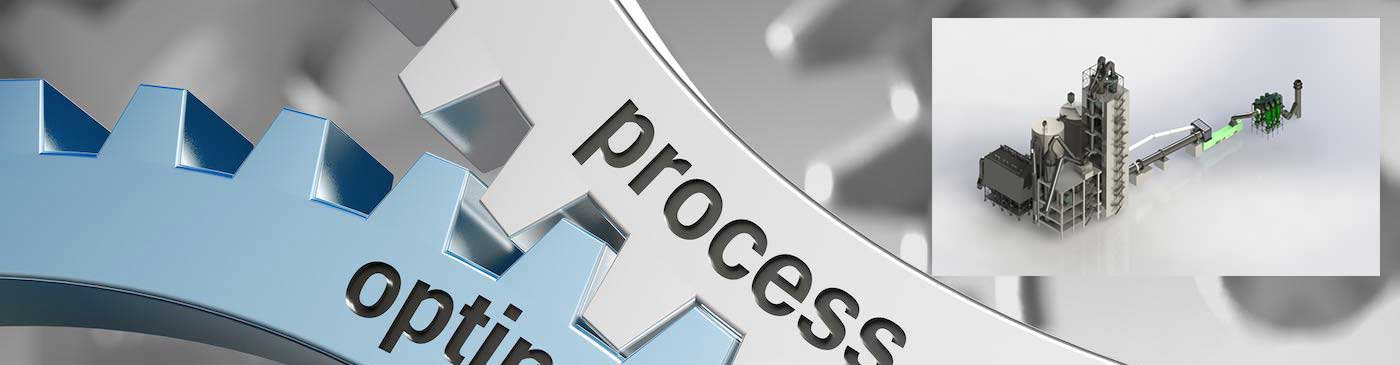
Production Process Control in Cement Plant
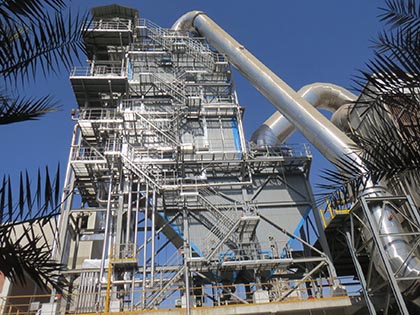
Taking the partial statistical data of cement product quality of a cement plant as an example, this article analyzes the main problems existing in the current production quality control of a cement plant. The average monthly compressive strength of cement products was 44.8mpa for 28d and 50.5mpa for 28d, and the coefficient of variation fluctuated between 3.0CV and 5.0CV. These data show that the stability of ex-factory cement products is poor, which is a major problem in the production quality control of cement plants. The stability of cement is one of its important properties, and it is also the main reference factor for customers to choose cement products. Poor stability directly affects the market competitiveness of cement products, and also affects the production efficiency of cement plants. Therefore, it is important to have good quality control of the cement plant, improve the production quality of cement plant and effectively control product quality by strengthening quality management and updating production technology.
Cement Plant Process Improvement Plan
- In order to improve cement quality of cement plant, we must first control the raw material source of cement plant. For raw materials were supplied by many clinker plants and the sources were complicated. According to the production needs of cement plants, the strength of incoming clinker should be controlled within the range of 28 ~32MPa, and 1 ~ 2 suppliers with strong supply capacity and stable quality of raw materials should be selected for long-term cooperation, so as to avoid unsteady supply of raw materials and uneven quality.
- Homogenization is a basic measure to ensure the quality of ex-factory cement and reduce consumption, and also an important way to stabilize the quality of ex-factory cement. Therefore, it is necessary to strengthen the pre-homogenization measures of clinker, expand the yard area, add more material piles, prevent segregation phenomenon and non-uniformity caused by small piles in the yard, and systematically evaluate the index of material uniformity.
-
The original cement plant has only one grinding mill and 2.4x 11.0m ball mill, the production capacity is seriously insufficient. In order to improve the quality control ability of the cement plant and respond to the national energy conservation, emission reduction and energy consumption reduction, this renovation aims at the current situation of backward technology and high energy consumption. According to the production situation of the cement plant, a series of transformation is carried out on the existing grinding system, and a small 3.8x 13.0m cement grinding unit with roller press is built.
- To make full use of the original clinker grinding plant, the active mixing material with poor easy grinding ability - water slag is pulverized separately, stored in the slag powder storehouse, and the microcomputer is used to prepare cement proportionally, which can achieve reasonable particle gradation and the effect of separate grinding.
- Optimize the homogenization measures of packaging cement and improve the multi-point feeding mode of homogenization warehouse; The outflow cone angle of homogenized powder storehouse was changed from 60 ° to 70 ° in the past, and the flow effect generated by the gravity of powder itself was used to homogenize powder in the storehouse. In addition, the bottom of the storehouse was transported by fluidized air chute, so as to achieve the maximum homogenization.
- The packaging machine will be changed to the multiple-mouth type, and the automatic loading system will be added. The production technology level of cement plant is improved through the improvement of host facilities, and the equipment configuration parameters are optimized. The cement plant production process is automatically controlled by microcomputer.
Cement Quality Control
In the process of cement milling, quality control mainly includes fineness, specific surface area and particle distribution control of cement. In cement grinding process, although the specific surface area needs to be measured every once in a while, it has no close correlation with the cement strength and cannot reflect the distribution of cement particles. Therefore, the specific surface area of cement shall not be used as the single factor on quality control of cement milling. The particle size distribution of cement clinker is mainly related to hydration degree, water-cement ratio and water requirement of standard consistency, while the particle size distribution of clinker and mixed material determines the closest packing density of cement particles, thus determining the strength of cement. Therefore, cement particle distribution is the key part of cement production quality control. When the cement fineness is relatively small, 80 and the sieve residue cannot reflect the grinding condition, so 32 or 45 & M should be used as the quality control standard.
Properties | Finess | Consistency | Initial Setting | Final Setting | 3d Strength/MPa | 28d Strength/MPa | Weight Qualified Rate /% | ||
---|---|---|---|---|---|---|---|---|---|
Year | /μm | /mm | /mim | /mim | Flexural | Compressive | Flexural | Compressive | |
Before the Optimisation | 3.8 | 28.8 | 205 | 285 | 4.6 | 25.3 | 7.4 | 46.8 | 100 |
2013 | 1.2 | 27.2 | 165 | 236 | 4.6 | 27.5 | 7.7 | 52.8 | 100 |
2014 | 0.9 | 27.4 | 110 | 195 | 4.7 | 27.8 | 7.6 | 51.5 | 100 |
2015 | 0.7 | 27.8 | 116 | 210 | 4.8 | 28 | 7.6 | 52.2 | 100 |
A comprehensive analyzer is needed to control the composition of raw materials. The instrument is composed of a composition analyzer and analysis computer. Composition analyzer is divided into offline calcium iron analyzer and TXD element analyzer, respectively to the raw material content of CaO and Fe2O3, AL2O3 and SiO3. Content determination of analyzer can quickly and timely get into the raw material of the homogenization yard. After raw materials and grinding cement were analyzed, the result will come out in a few minutes, then adjust the raw materials according to the result.