Homogenization Silo for Cement Production Line

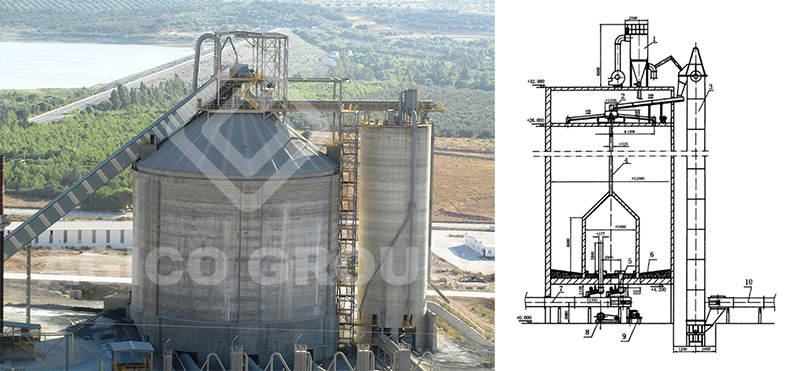
Continuous Homogenization Silo Working Principle
Raw material is continuously fed from the top of the reservoir, the continuous homogenization silo is continuously discharged while being aerated and agitated, as it is fed to the central chamber in turn when discharging. The materials in the mixing chamber are further mixed due to the continuous inflation of the mixing chamber, so that the qualified raw materials are discharged from the high-level overflow pipe, and the continuous homogenization of the excess gas is discharged from the exhaust pipe to the outer ring zone, and the silo is disposed at the center position. A cylindrical mixing chamber to reduce the discharge pressure in the reservoir and eliminate the funnel flow.
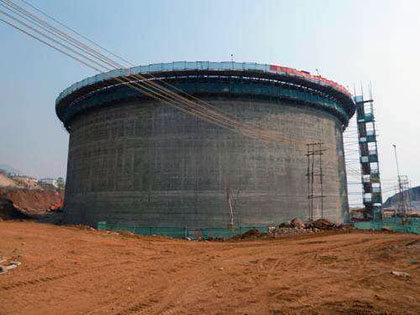
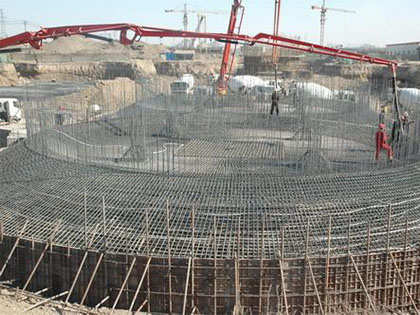
The crushed limestone can be stored in a conditional storage tank, and the homogenization reservoir can be used for storing the powdery loose material with a central cone-shaped cantilever cylindrical tube magazine. Limestone can also be stored in the cylinder silo, and the storage tank can be build with reinforcing steel or prestressed concrete, steel structure.
The homogenization silo can be divided into types of single or multi-barrel storage, large storage and round storage. The homogenization silo proves that it can effectively store granular loose materials, clinker and broken limestone. It can also effectively storage of powdery loose materials, in the cement production process, in order to ensure the smooth progress of the production process, homogenization of loose materials, broken limestone, cement raw materials, cement clinker, homogenization of different varieties. It is necessary to store the cement and the mixed materials, etc., and to homogenize silo storage capacity is large.
Tips for continuous homogenization silo design:
- Each process production line should be equipped with 1 or 2 continuous homogenization silos, and the height to diameter ratio should be 2 to 2.5.
- The raw material moisture in the storage should be controlled below 0.5%, and the maximum should not exceed 0.8%.
- Do not mix large particles of raw materials, abrasive bodies and other debris in the raw materials. It has been proved that raw material homogenization silo can maintain long-term, reliable and effective operation, which can be affected by control of raw material moisture. The raw material with water content below 0.5% has good flow performance. When the water is increased, the fluidity of the raw material is lowered, and the bottom of the reservoir and the wall of the reservoir are easy to be caked, thereby reducing the effect of gravity mixing and gas equalization, and the inclusion of impurities such as the grinding body is likely to block the unloading device.
- Raw material storage should be evenly dispersed. Raw material feeding adopts the top-of-stock raw material distributor and multi-point feeding to disperse the raw material. The larger diameter continuous raw material homogenization silo adopts multi-point storage, and the small diameter continuous homogenization silo can also be used for single point storage.
- The design of the inflation system should reduce the resistance. The arrangement of the inflatable box should reduce the inflation dead zone in the warehouse, and select the gas permeable layer material with good air permeability, uniform air distribution and wear resistance. The gas box and piping system must be well sealed.
- The constant-capacity blower should be used for air supply, and the blower should be spare. Constant-capacity rotary blower does not change the air volume due to changes in system resistance, so it is suitable as a gas source for continuous homogenization. The amount of inflation is determined according to the type of the bottom of the reservoir, and the inflation pressure is preferably 60 to 90 kPa.
- Air distribution equipment for continuous homogenization of the bottom of the silo should use air distributor, solenoid valve, pneumatic or electric butterfly valve.
- The continuous homogenization silo can be discharged from the bottom of the silo or the side of the silo. Each warehouse should have two or more discharge doors. The unloading device equipped with manual maintenance gates, quick opening and closing valves and flow control valves is used to discharge the materials. Clearing the silo is more advantageous.
- In the cold or rainy areas, the continuous homogenization warehouse should be set up in the warehouse. Between the top of the silo and the preheater tower, the walkway can be set if available.
- The continuous homogenization silo should have a delivery circuit for returning the raw materials to the warehouse. In this way, the continuous homogenization silo and the kiln feed can be used for the strip test operation when the system is put into use or the kiln is shut down.