Magnesium Oxide Kiln
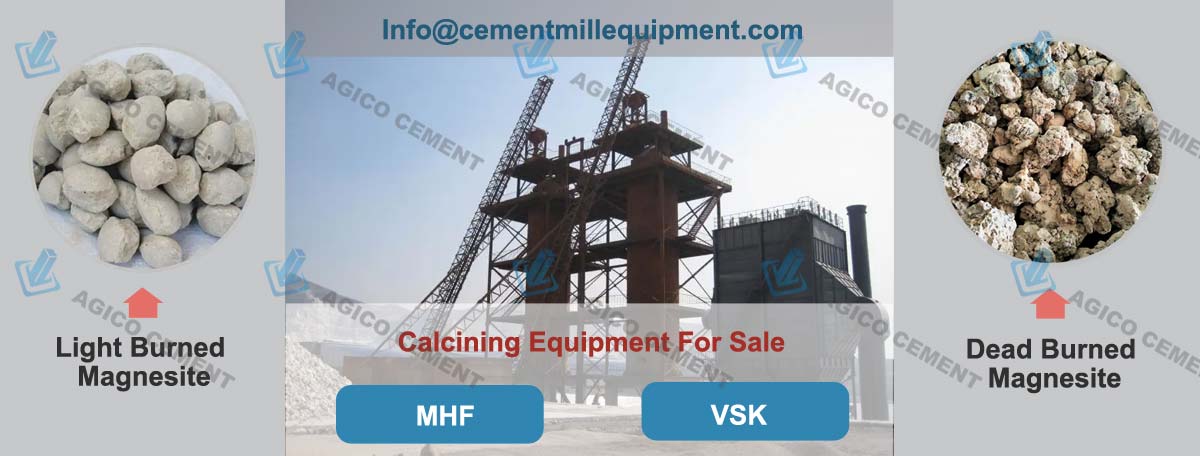
Magnesite Calcining Kiln Types - MHF & VSK
AGICO focuses on developing light burned and dead burned magnesite calcining technology, and has been manufacturing calcining equipment such as multiple hearth furnaces (MHF)and gas-fired vertical shaft kiln, which are precisely adapted to the calcining process of magnesite. Calcining kilns and furnaces are manufactured with environmentally friendly and energy-saving design, fully automated control and modular structure, they meet the industrial production needs of light-burned magnesia (700~900 ℃) and heavy-burned magnesia (1500~1800 ℃ ), AGICO is aimed to help customers achieve cost reduction, efficiency improvement and green transformation in magnesite calcining plant.
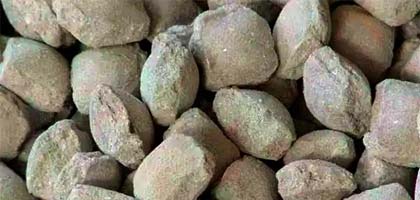
Light Burned Magnesite
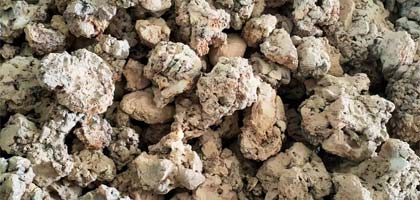
Dead Burned Magnesite
Calcining Kilns Available from AGICO:
AGICO can design and construct of MHF and vertical shaft kilns for magnesite calcining production. AGICO can also offer vertical shaft kilns of various types such as: kaolin gas-fired vertical shaft kiln, bauxite gas-fired vertical furnace, plate-shaped corundum gas-fired vertical furnace, synthetic magnesia-calcium sand high-temperature vertical shaft kiln, gas-fired dolomite and lime light-fired vertical shaft kiln, natural gas vertical shaft kiln gas burners, high-temperature vertical shaft kiln flue gas purification system, natural gas vertical furnace control system, etc.
Caustic Calcined Magnesite Calcining: Multiple Hearth Furnace
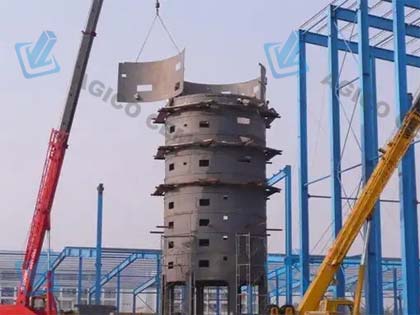
Applicable raw materials: 0~30mm particle size magnesite
Core Technology:
- Multi-layer precise temperature control: adopting a multi-chamber layered structure, each layer independently adjusts the temperature and residence time to ensure uniform calcination of materials and the decomposition rate of active magnesium oxide ≥98%.
- Fully enclosed operation: Enclosed feeding and unloading system, with high-efficiency bag dust removal, dust escape rate ≤10mg/m³, in line with strict environmental protection standards.
- Waste heat recycling: The high-temperature flue gas from the kiln roof is used to preheat the combustion air through a heat exchanger, which increases the overall thermal efficiency by 25% and reduces energy consumption by 30%.
Equipment advantages :
- Energy saving and high efficiency: gas direct combustion design, high fuel utilization rate, energy consumption per ton of product is 15%~20% lower than that of traditional kilns.
- Automatic control: PLC intelligent system monitors temperature, material level and pressure in real time to realize unmanned operation.
- Strong durability: The refractory lining is made of high-aluminum composite material, which has excellent thermal shock resistance and a service life of more than 8 years.
Dead Burnt Magnesite Calcining: Gas Fired Vertical Shaft Kiln
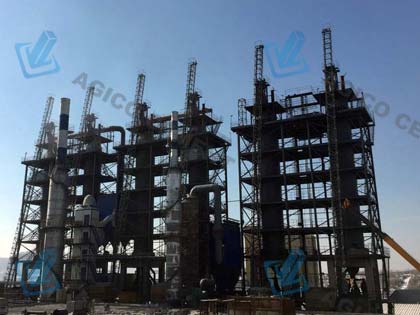
Applicable raw materials: 30~300mm block magnesite
Core Technology:
- High temperature densification calcination: Using natural gas/coal gas as fuel, the high temperature zone in the kiln can reach 1800 ℃ , which makes the magnesite completely decompose into high-purity periclase crystals, and the product density is ≥3.5g/cm³.
- Uniform combustion design: Multiple rows of sleeve burners are distributed along the circumference of the kiln body, with staggered layout up and down to ensure uniform cross-sectional temperature (temperature difference ≤±15 ℃ ).
- Heat recovery system: The waste heat of verticle shaft kiln gas is recovered through the air preheater and the gas heat exchanger, and the combustion air is preheated to above 500 °C , with an energy saving rate of over 20%.
Core advantages:
- Flexible fuel adaptability: supports a variety of clean fuels such as natural gas, coke oven gas, and mixed gas.
- Stable and reliable structure: vertical closed kiln body, multi-layer refractory insulation structure (refractory bricks + aluminum silicate fiber + steel shell), heat dissipation loss ≤5%.
- Intelligent unloading control: The spiral cone ash discharging machine is linked with the tubular valve to discharge materials continuously and evenly, avoiding air flow disturbance in the kiln.
Comparison of Multiple-hearth Furnace & Vertical Shaft Kiln
Characteristic | Light Burning Multiple-hearth Furnace | Dead Burning Gas Fired Vertical Shaft Kiln |
---|---|---|
Calcination temperature | 700~900℃ | 1500~1800℃ |
Product Usage | Building material additives, rubber fillers, environmentally friendly materials | Refractory products, metallurgical furnace linings, high temperature ceramics |
Energy consumption index | Gas consumption ≤80m³/ton product | Thermal efficiency ≥ 65%, fuel cost is 25% lower than traditional kilns |
Environmental performance | Dust emission ≤10mg/m³, unorganized emission approaches zero | Low nitrogen combustion technology, NOx emission ≤100mg/m³ |
Degree of automation | Full process PLC control, support remote monitoring | Intelligent temperature control system, fault self-diagnosis function |
Magnesium Oxide Manufacturing Process
The manufacturing process of light-burned and dead-burned magnesium oxide is different, which can be affected by the calcinating temperature, fuel and calcinating equipment. Here are the basic manufacturing process steps of magnesium oxide production.
Light-burned magnesium oxide process :
raw material crushing → multi-chamber furnace layered calcination (700~900 ℃ ) → grinding and screening → active light-burned magnesium powder
Dead-burned magnesium oxide process :
lump ore pretreatment → gas-fired vertical kiln high temperature calcination (1500~1800 ℃ ) → crushing and screening → high-density dead-burned magnesia
-
Raw material pretreatment (Ore selection and crushing)
High-grade magnesite (MgCO₃ content ≥ 45%) is used, which is initially crushed into 30~300mm blocks by a jaw crusher to remove impurities and low-grade ores. -
High Temperature Calcination in Gas-fired Vertical Shaft Kiln
Adopts a gas-fired mechanized vertical kiln. The kiln body is composed of refractory bricks, insulation layer and steel shell, equipped with multiple rows of sleeve burners, and the fuel is natural gas or coal gas. -
Cooling and Discharging
The high-temperature magnesium oxide (about 1600 ℃ ) after calcination is continuously discharged through the screw cone ash discharger at the bottom of the kiln and enters the closed cooling bin: -
Finished Magnesium Oxide Grinding, Screening
- Crushing and grinding: The cooled blocky heavy-burned magnesia sand is first crushed by a jaw crusher to crush the material into uniform particles <50mm; then it enters the fine grinding stage, using a high-efficiency ball mill or vertical roller mill for deep grinding, strictly controlling the finished product particle size below 0.088mm (180 mesh), fully meeting the stringent requirements of refractory materials for fineness and uniformity.
- Screening and grading: The ground materials are accurately graded through multi-layer vibrating screens or airflow separators to separate qualified particle size products of 0.045~0.088mm (325~180 mesh), and coarse particles and residual impurities are removed simultaneously to ensure the purity of the finished product;
- Finished product processing and packaging: The graded heavy-burned magnesia is sealed and packaged in ton bags or customized small specifications according to customer needs. Each batch is accompanied by an authoritative test report (including core indicators such as MgO content ≥92%, volume density ≥3.5g/cm³), ensuring product traceability and terminal application performance.
This manufacturing process achieves efficient and continuous production through mechanized and automated equipment, combining precise particle size control and quality stability, providing high value-added raw material guarantees for downstream refractory materials, metallurgy and other industries.
Advanced Designs in Magnesium Oxide Production Line
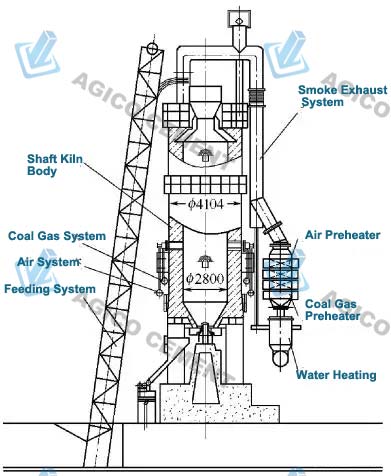
Magnesium Oxide Production Lines are designed with the concept of environmental protection and energy saving, if you are looking for magnesium oxide production equipment, contact AGICO now for detailed solutions.
- Ultra-low emission: integrated cyclone dust removal + bag filtration + flue gas recirculation technology, particulate matter and harmful gas emissions are far below national standards.
- Efficient utilization of resources: The waste heat from calcination exhaust gas is recovered to preheat fuel and combustion air, increasing the overall energy efficiency of the system by 30%.
- Green production: The kiln is fully enclosed, free of dust and noise pollution, and the factory environment is friendly.
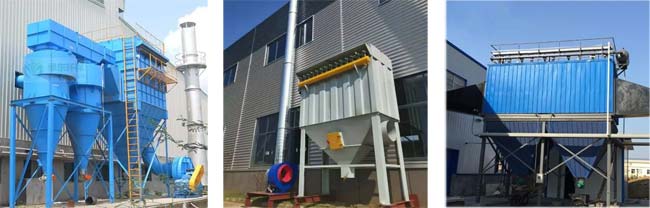
Magnesite Calcining Kiln Application Cases
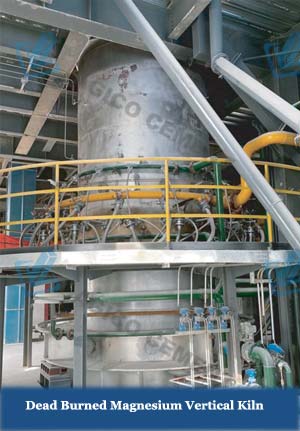
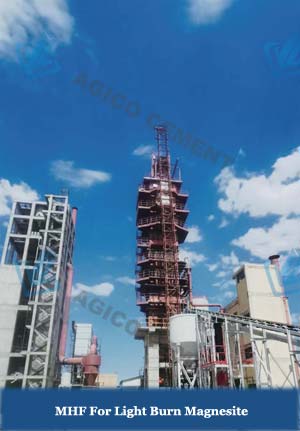
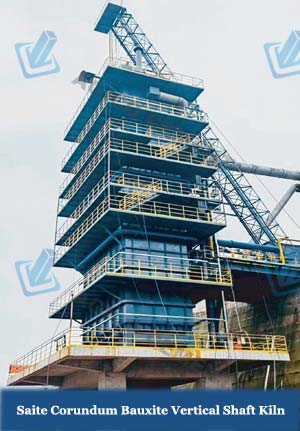
- A magnesium company in Liaoning: It adopts a multiple hearth kiln as light-burning magnesium oxide production line, with an annual output of 50,000 tons of light-burned magnesium powder. The product activity reaches 140s (citric acid method), and the comprehensive energy consumption is reduced by 18%.
- A refractory material factory in Henan: equipped with a gas-fired vertical shaft kiln re-firing system, the output magnesia volume density ≥3.52g/cm³, the high-grade Dead-burned magnesium oxide products are exported to high-end markets in Europe and the United States.